With a history that dates back to 1962 and a firmly entrenched position as a “core” Rickenbacker model, you might be surprised to learn that the “Deluxe” 620 and its “Standard” little brother 610 were actually not big sellers over their first twenty or so years. In fact, the line was probably on its way to discontinuation before a rediscovered 1963 prototype graced the cover of a 1979 album. That little bit of luck kicked off a surge in demand that has lasted to this day. But we’re getting ahead of ourselves! To talk about the 610/620, you have to start with the 450.
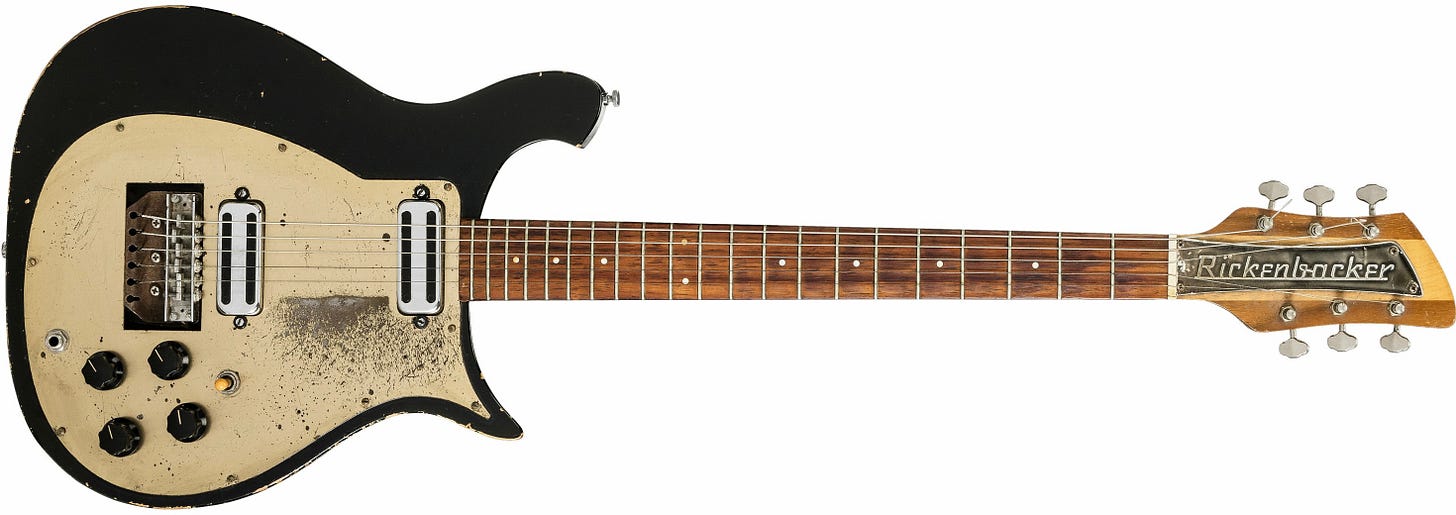
The “cresting wave” body shape debuted on the 450 and 425 in 1958, an evolution of the original 1956 Combo 400’s “tulip” body. You can and should read all about the evolution of the 450 here. While the 450 was an entry-level guitar, the body was too distinctive to not take up-market. Enter the 615/625. Raising the deck height of the 450 from 3/8” to the 3/4” found on the semihollow guitars created enough room to move the pickups from recessed/pickguard mounted to topmounted and to fit a standard 6-saddle adjustable bridge with Accent vibrato—and raise the price of the Standard 615 by $80 (almost $850 in 2025 dollars) from the entry level 450 and $110 (about $1,165 in 2025 dollars) on the Deluxe 625. A future classic was born…although it would take a while to cement that status.
1962
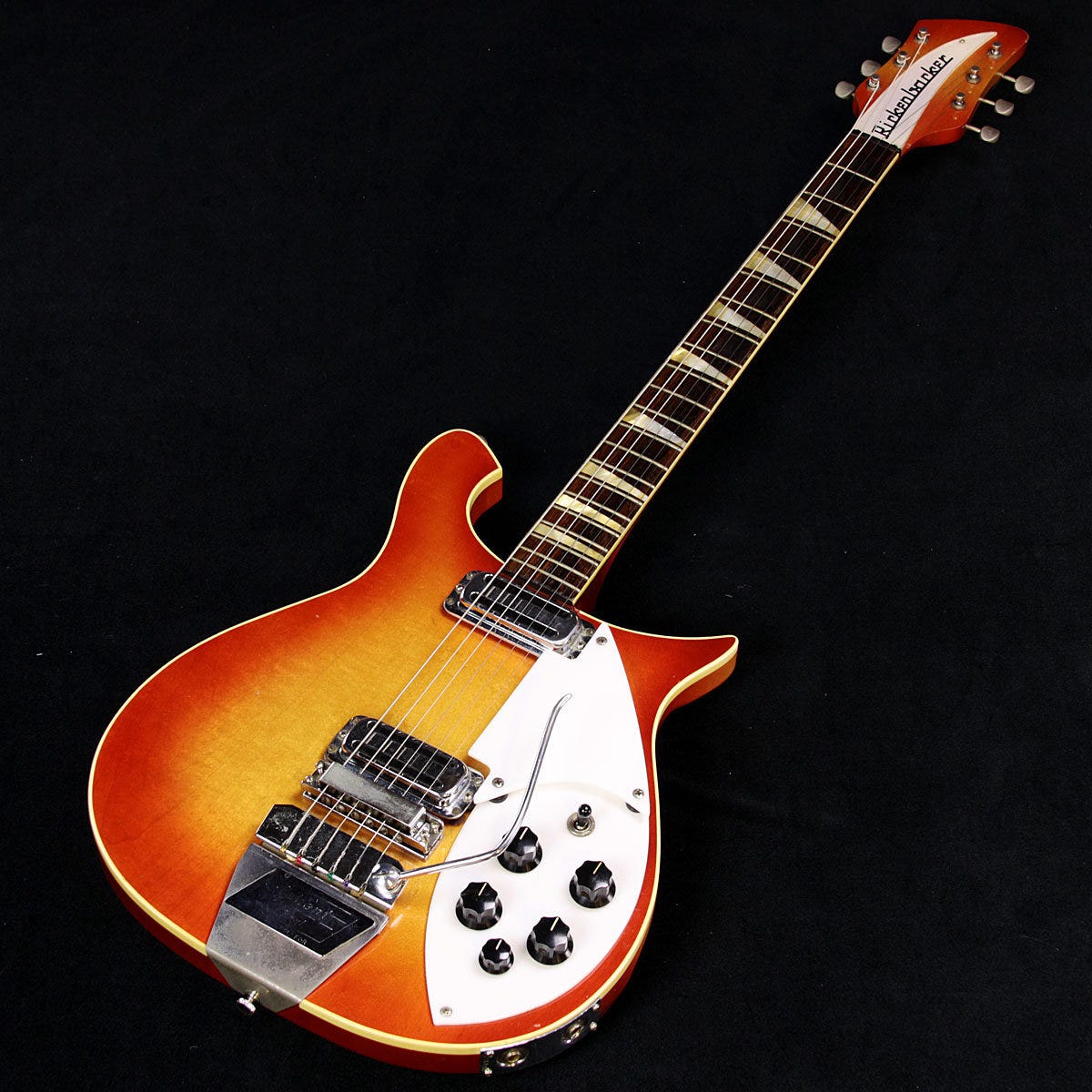
Production began in January on the 625. The Deluxe 625 was offered in Black, Natural, and Fireglow (the Jetglo/Mapleglo/Fireglo names we’re familar with did not become standard until 1967. You can read all about Rickenbacker factory colors here). It featured solid maple body wings with cresting wave upper/pointed lower cutaways and a bound top, a bound 21 fret one-piece maple through neck with poured resin full width triangle inlays and a paddle headstock with walnut wings—although by March the headstock wings would switch to maple.
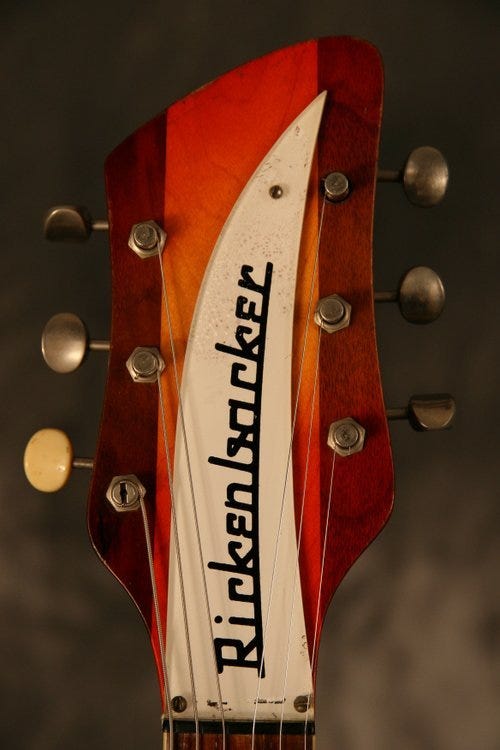
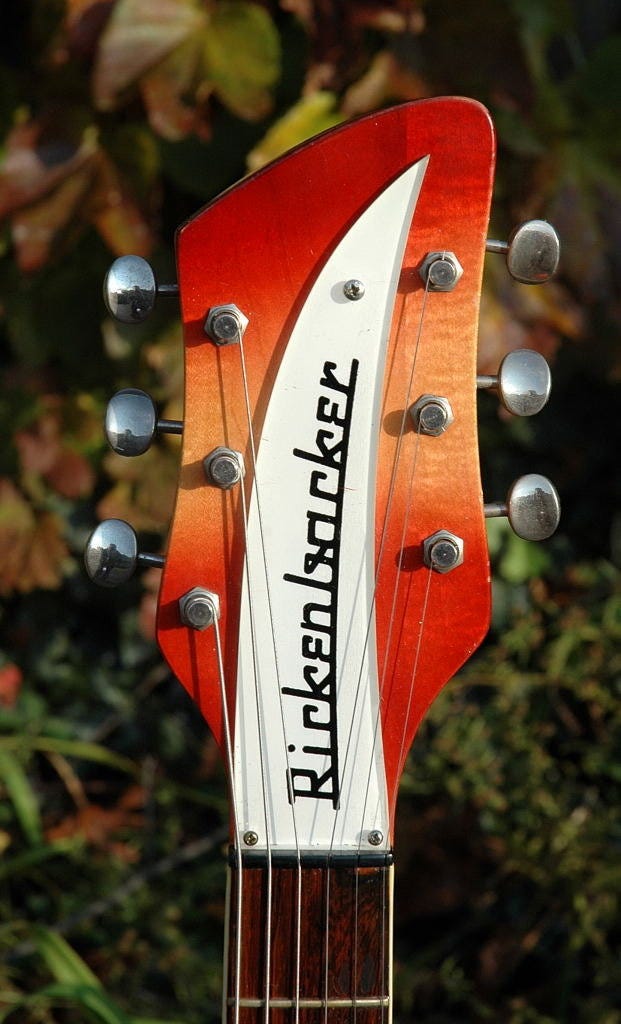
Tuners as standard were nickel bean button single line Kluson Deluxes, although you will find many 1960s 625s with pearloid Van Ghent tuners. The 625 featured 2 top mounted toaster pickups and an “Accent by Paul” vibrato with 6 saddle adjustable roller bridge. Controls were of the standard 5 knob/1 selector switch variety, mounted on a two-level teardrop pickguard, with mono/stereo wiring with side output jacks
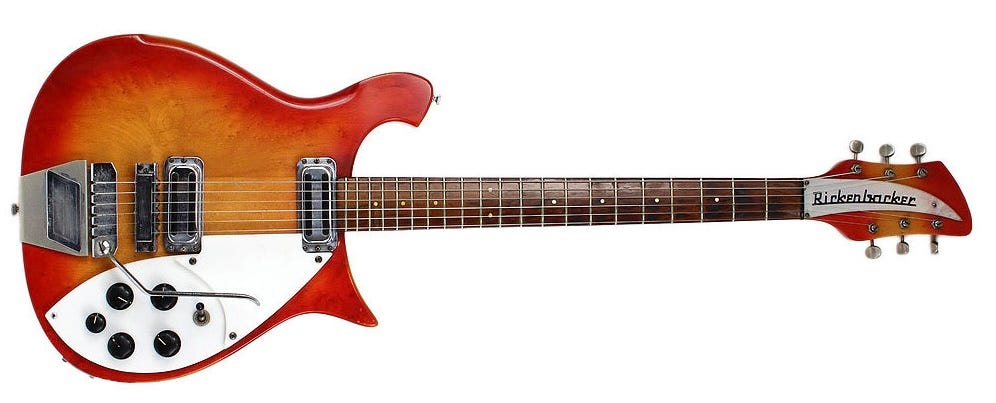
The Standard 615 was available in Fireglow only, and lost the 625’s binding, triangle inlays, and stereo output. The top edge was contoured for player comfort, and the inlays were simple dots. All other features were identical to the 625. Production began in November.
1963
Midway through 1963, the Accent vibrato equipped on all Rickenbacker models with a vibrato—including the 625 and 615—began losing the “Ac’cent by Paul” plaque. While you will find examples still thusly equipped through the end of 1963, by early 1964 the “plain” Accent was the default.
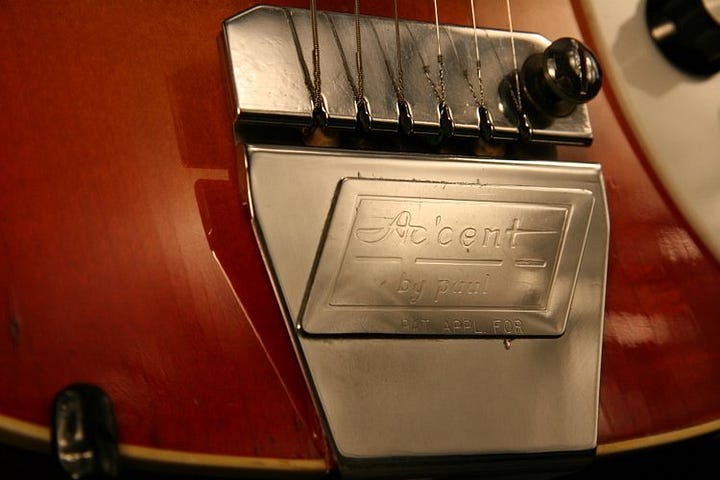
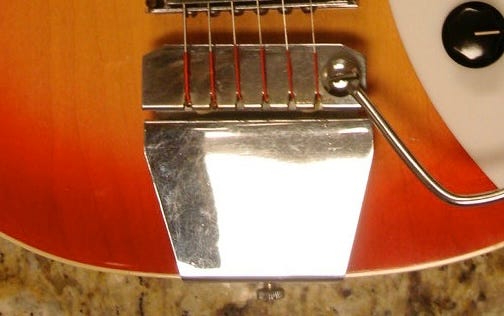
In 1963 Rickenbacker began experimenting with 12-string electric guitars. The first, the “Suzi Arden” 360/12 OS, was produced in July. The second, produced in December, was a 360/12 OS that was presented to George Harrison in 1964 by FC Hall that you likely have a reproduction of. The final was a 625/12 that was largely forgotten until 1979…and we’ll talk about its importance then.
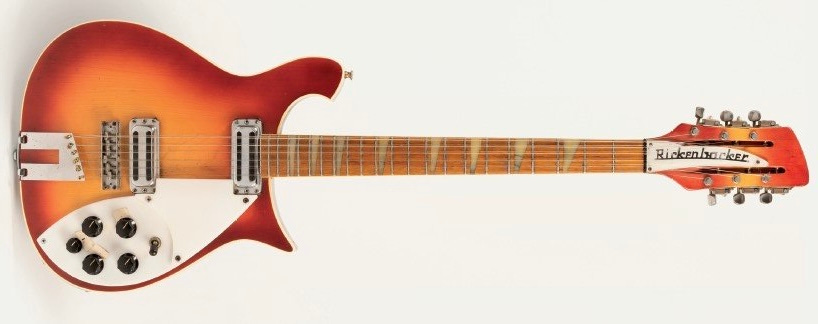
At the very end of 1963, Kluson changed the Deluxe tuner backs from “single line” to “double line”. At the same time the bushings changed from hex to round. Late 1963 to early 1964 saw a mixture of both tuners—as well as the Van Ghents.
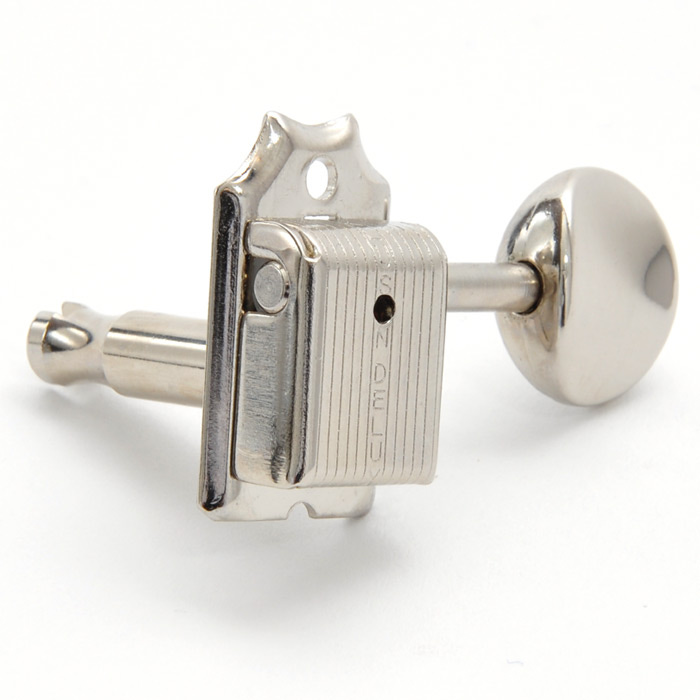
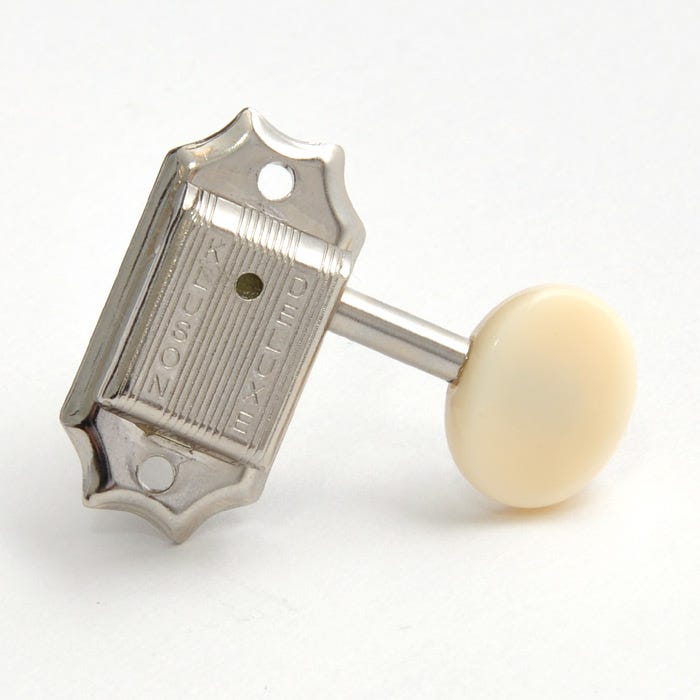
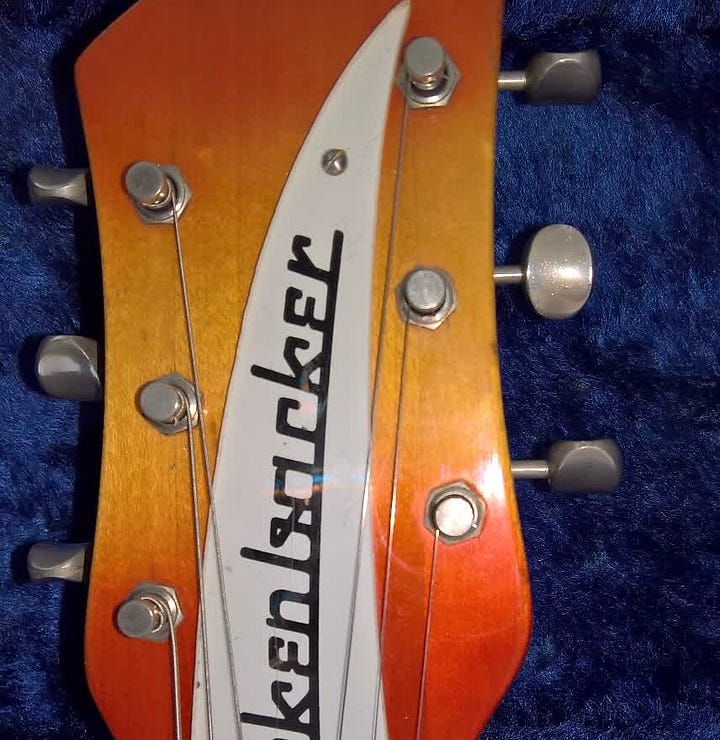
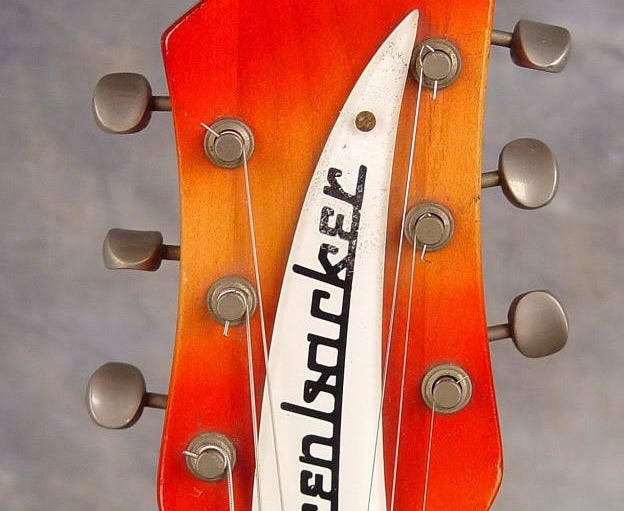
1964
1964 saw a number of minor changes to the 625 and 615. To start, the heel on the 625 and 615 changed from square to rounded.
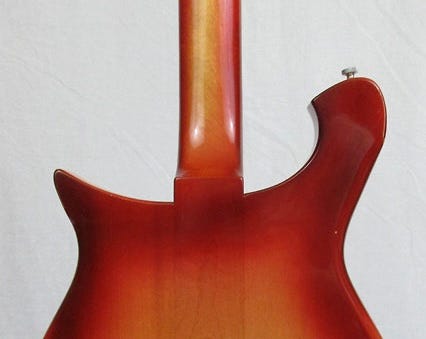
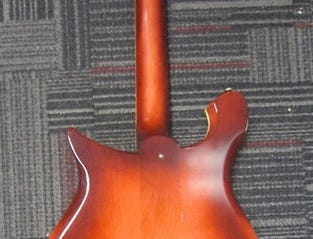
With the launch of the “New Style” rounded top 360 in early 1964, the triangle inlays on all “Deluxe” guitars—including the 625–would change from the older full width poured pearlescent resin to crushed pearl.
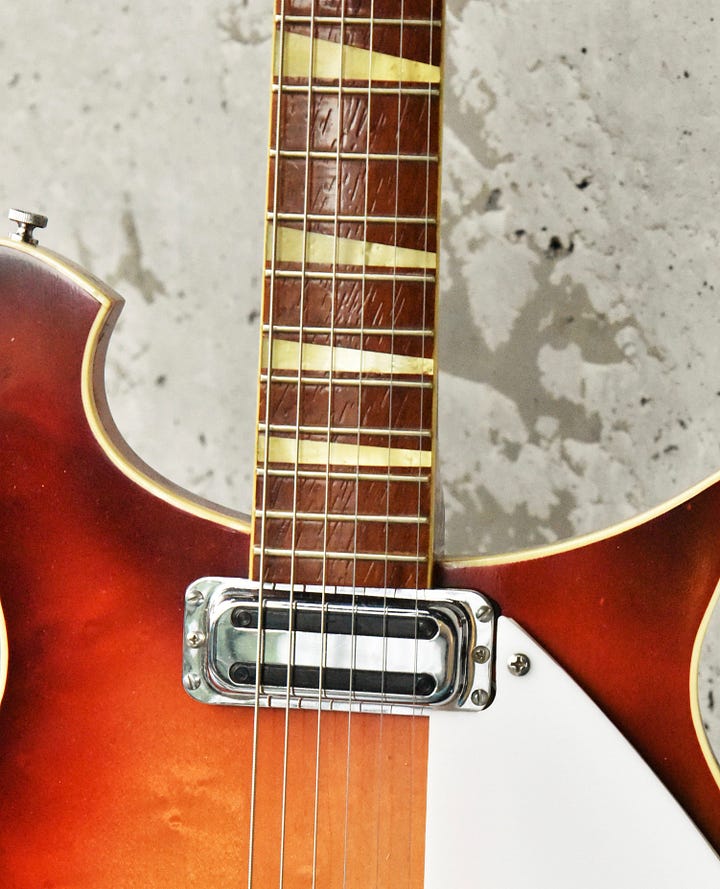
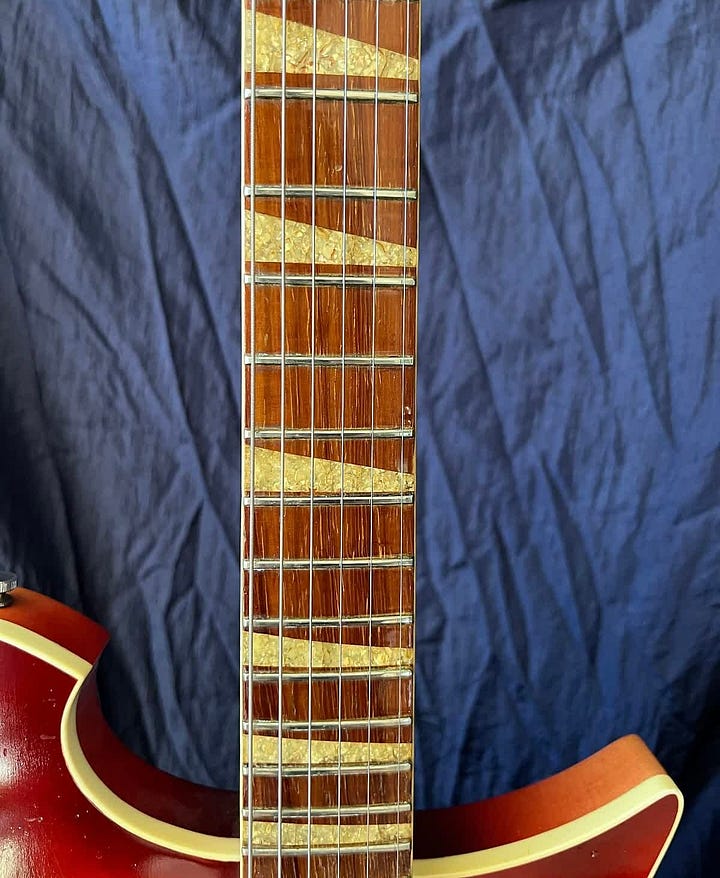
In late 1963 the headstock on all Rickenbacker guitars had begun shrinking slightly, losing about 1/8” in width. This change would appear on the 625 and 615 in early 1964.
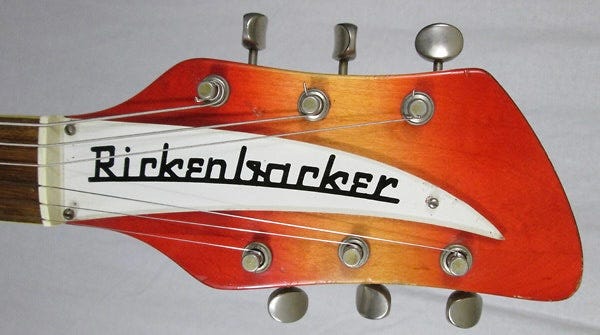
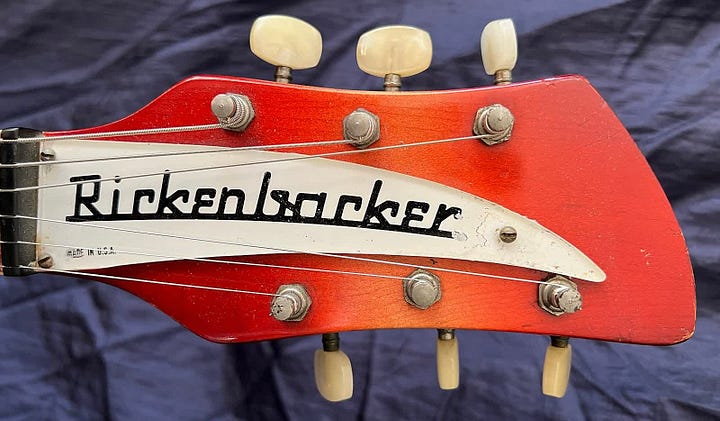
At British distributor Rose Morris’s request, “MADE IN U.S.A.” was added to the backpainted plexi truss rod cover. It would be printed parallel and below “Rickenbacker” for all models, including the 625 and 615.
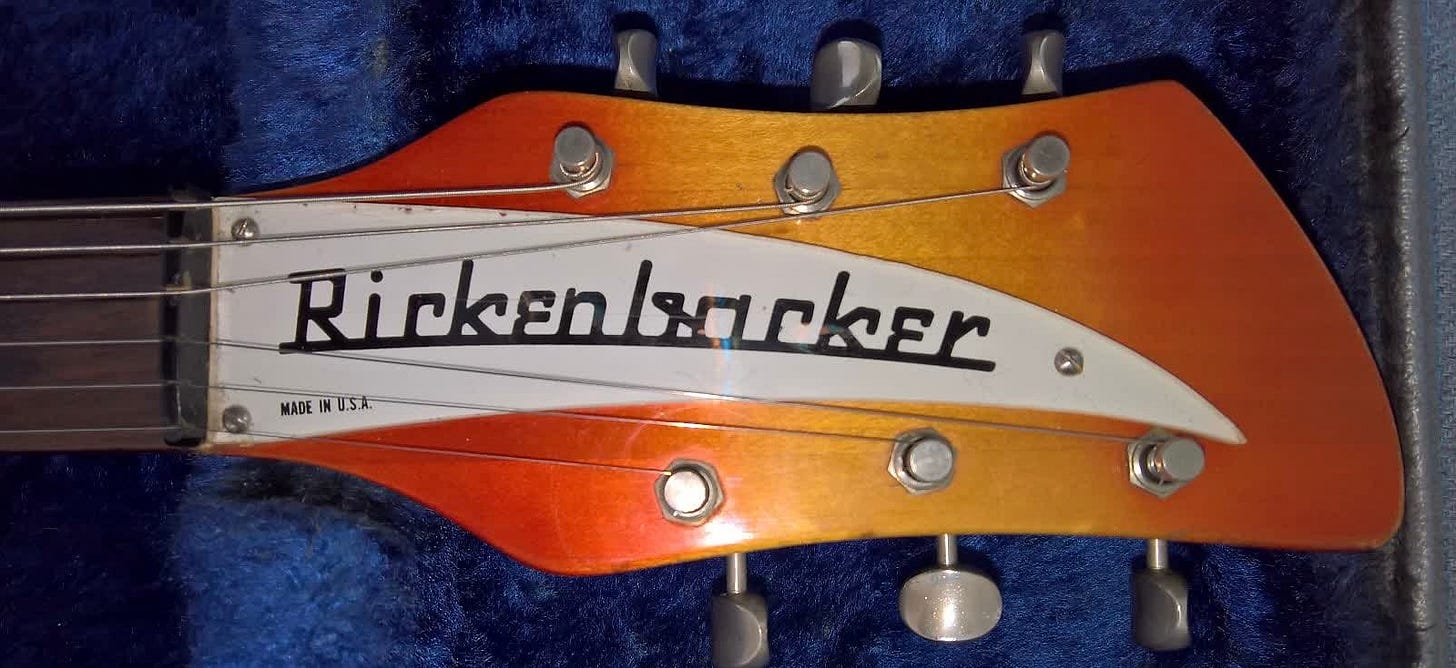
And speaking of Rose Morris, the 615 was one of the six Rickenbacker models they selected to import and sell in the United Kingdom. Unlike the semi-hollowbody guitars that got a special f-hole soundhole, the 615 (designated the Model 1995 for Rose Morris) was unchanged for the UK market. Offered only in Fireglow, it was…not a success, and no additional orders for the 615/1995 were placed by Rose Morris after 1964.
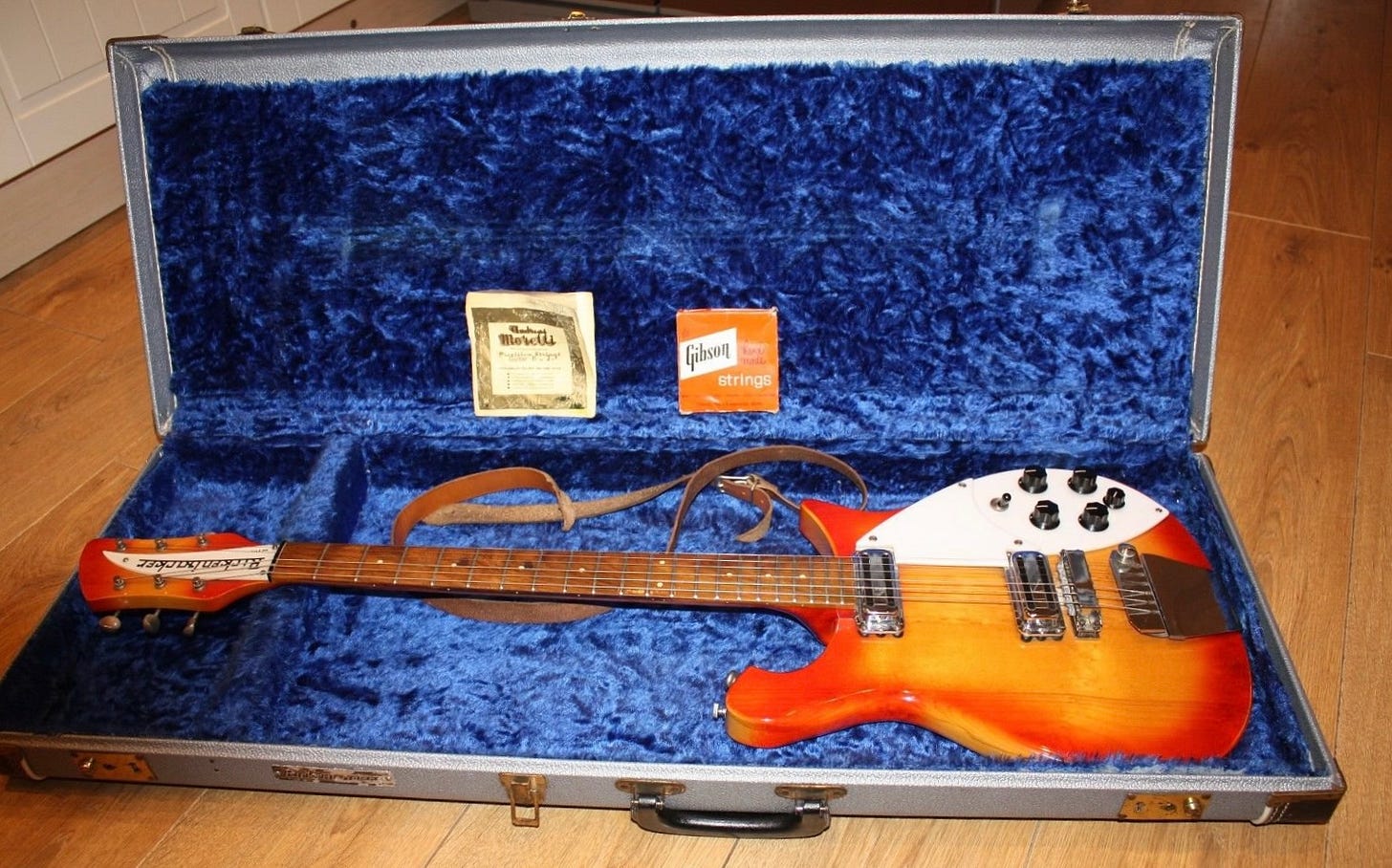
In mid-June, the control knobs on the 625 (but NOT the 615) switched from the black “vintage” style knobs to the new silver top knobs first seen on the “New Style” 360. The first version of these knobs had no labels and a dash indicator on the top.
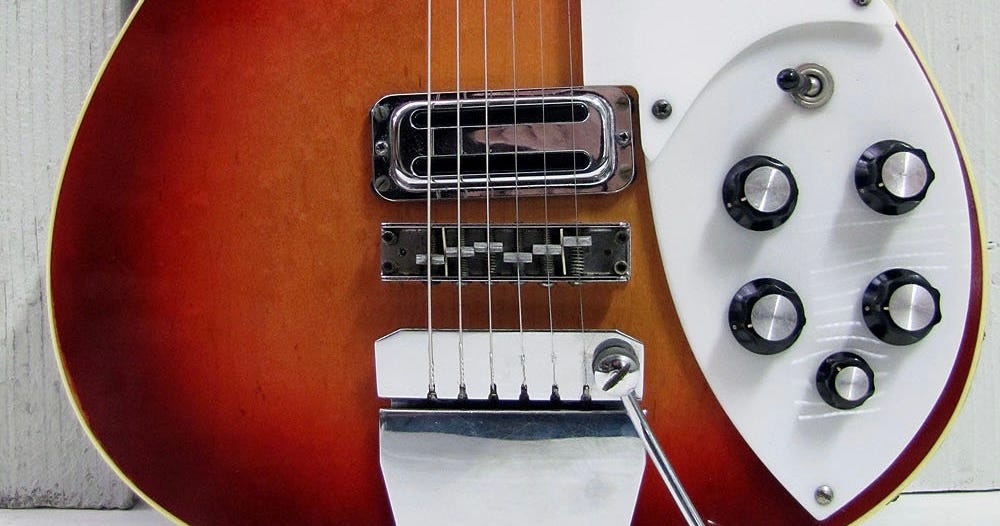
At least one—and maybe two—more 620/12s were produced in November, but the model was still not a “production” guitar. According to the Richard Smith book, another was made in 1969, but it has not surfaced. The model would not be made again or added to the pricelist until 1980.
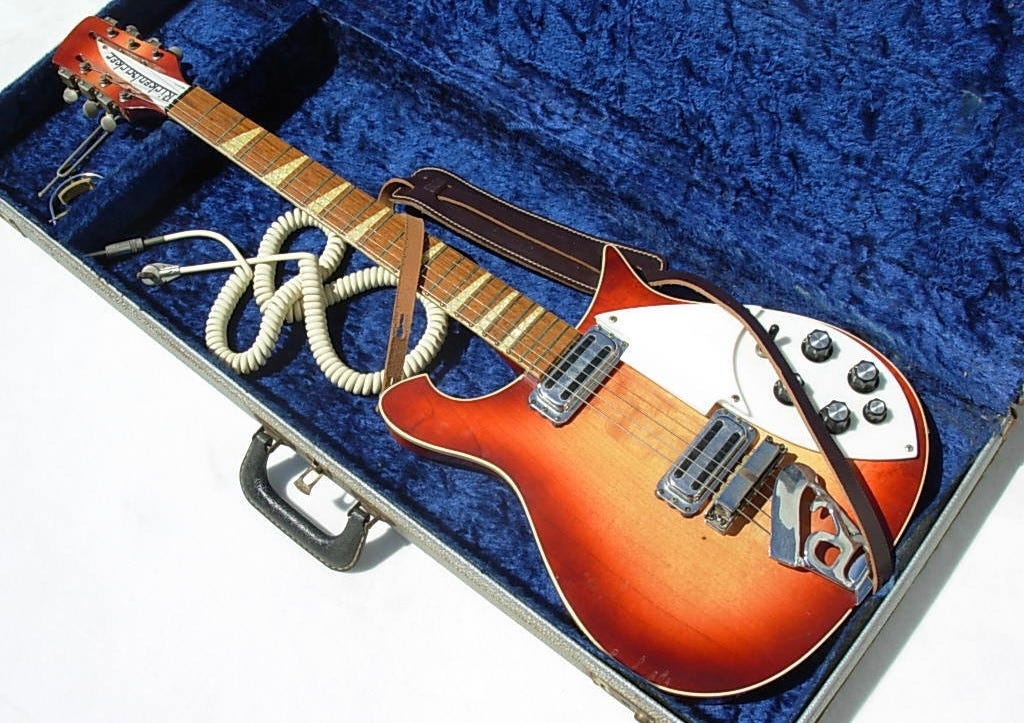
1964 would prove to be the high water mark of 620/610 production until 1980.
1965
While other guitars had received the now-familiar BASS/TREBLE TONE/VOLUME labels in August of 1964, for reasons unknown the 625 kept the plain-top knobs until October of 1965 when they too got the labeled, dash-top version. The 615 still wore the black vintage knobs.
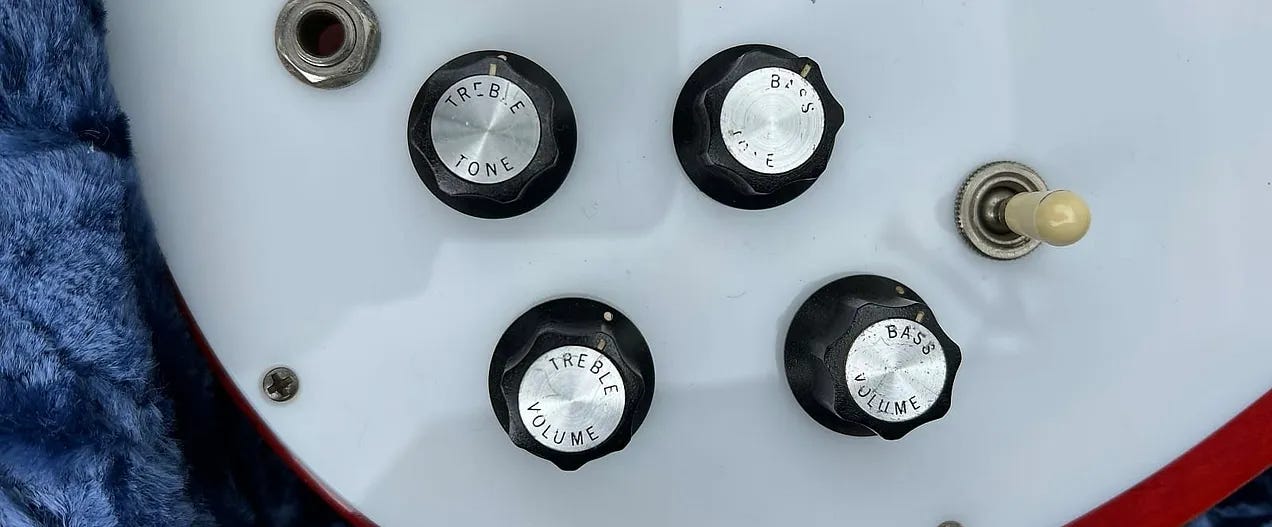
1967
In April the 615 finally got silver top knobs—the final “label/dot top” version. Knobs on the 625 (and all models!) also changed to the “dot top”.
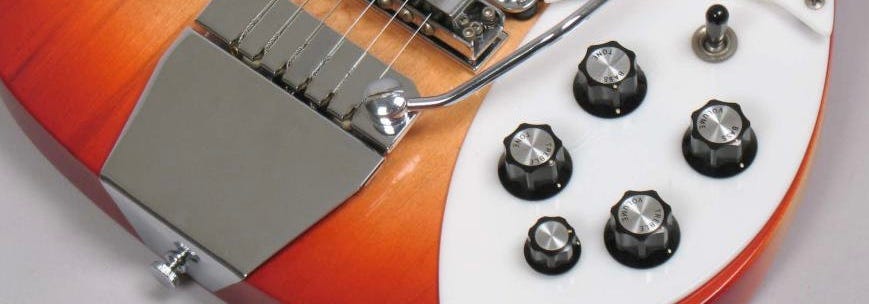
1968
In mid to late 1968 the “MADE IN U.S.A.” imprint on all plexi truss rod covers would move from being below and parallel to the Rickenbacker logo to being perpendicular to the logo, above the nut. On higher volume models like the 360 and 365, the model number would also be added to the truss rod cover, above the “MADE IN U.S.A.” Lower volume models, like the 625 and 615, did not get their model number printed.
Around the same time, the nut changed from a black phenolic material to white.

1969
In 1969, the license for the Accent vibrato Rickenbacker had used since 1960 (designed by Paul Barth, thus the original “Ac’cent by Paul” plate) expired. By the end of the 1960s the Accent had become quite dated and demand had dropped dramatically. Rickenbacker chose not to renew the license or find a replacement. While the pricelists would continue to include the vibrato equipped 625 and 615 until 1974, none would be produced after 1969. A handful of vibrato equipped semihollow guitars would be produced in 1970—probably special orders using leftover parts—but the -5 vibrato era at Rickenbacker was over. Despite that, some vibrato equipped models remained on the pricelist as late as 1977! To learn more about about zombie guitars and vaporware, click here.
Despite remaining on the price list until 1974 (along with the 625), the end of the Accent in 1969 was also the end of the standard 610/615. None would be produced until the model was (kinda!) reintroduced in 1984. The very last few 610s produced were equipped with first generation Higain pickups—distinguishable by their threaded stock polepieces.
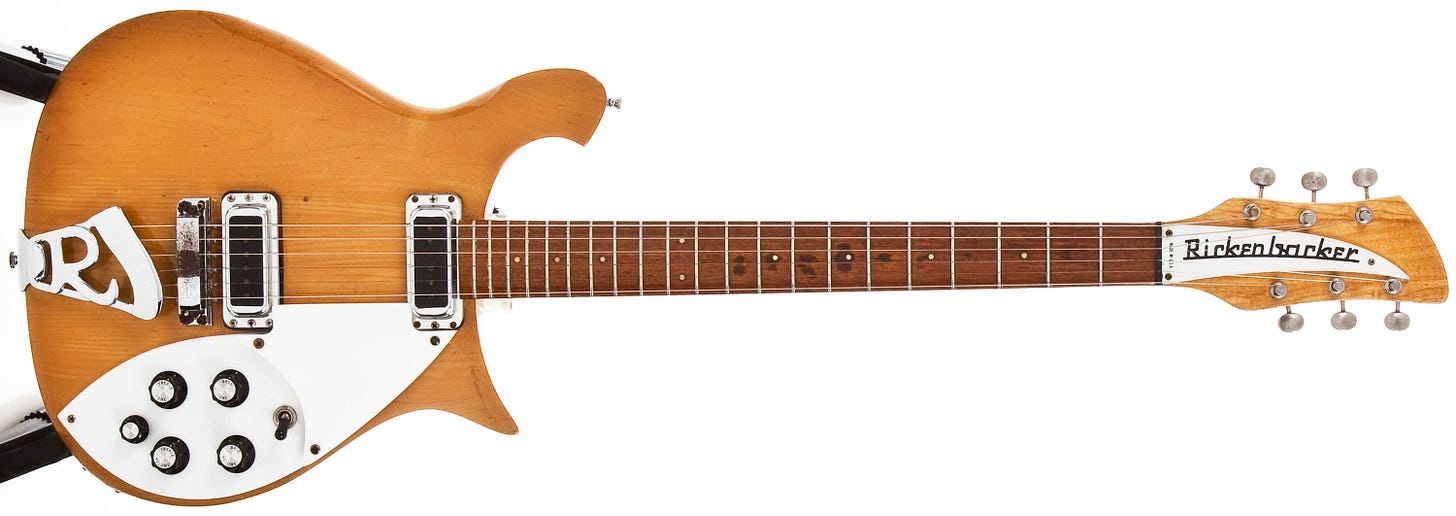
1973
The problem with documenting changes to the 620 during the 1970s is that there just weren’t that many built. While we can’t pinpoint exact change dates, we can use higher volume models to provide approximations. So that’s what we’re going to do.
While the non-vibrato equipped 620 would not appear on the pricelist or enter production at scale until 1973, a handful of special order guitars were produced between 1970-1972. The early 1973 production 620s were more or less identical to the last 1969 production 625s, with only a couple key differences. First, the Accent vibrato and 6-saddle roller bridge were (obviously) replaced by an “R” tailpiece and standard 6-saddle adjustable bridge.
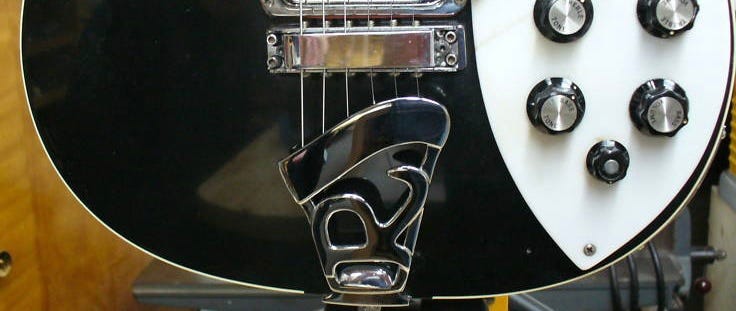
Additionally, guitars from early 1973 featured the same first-gen Higains found on the last 1969 615s.
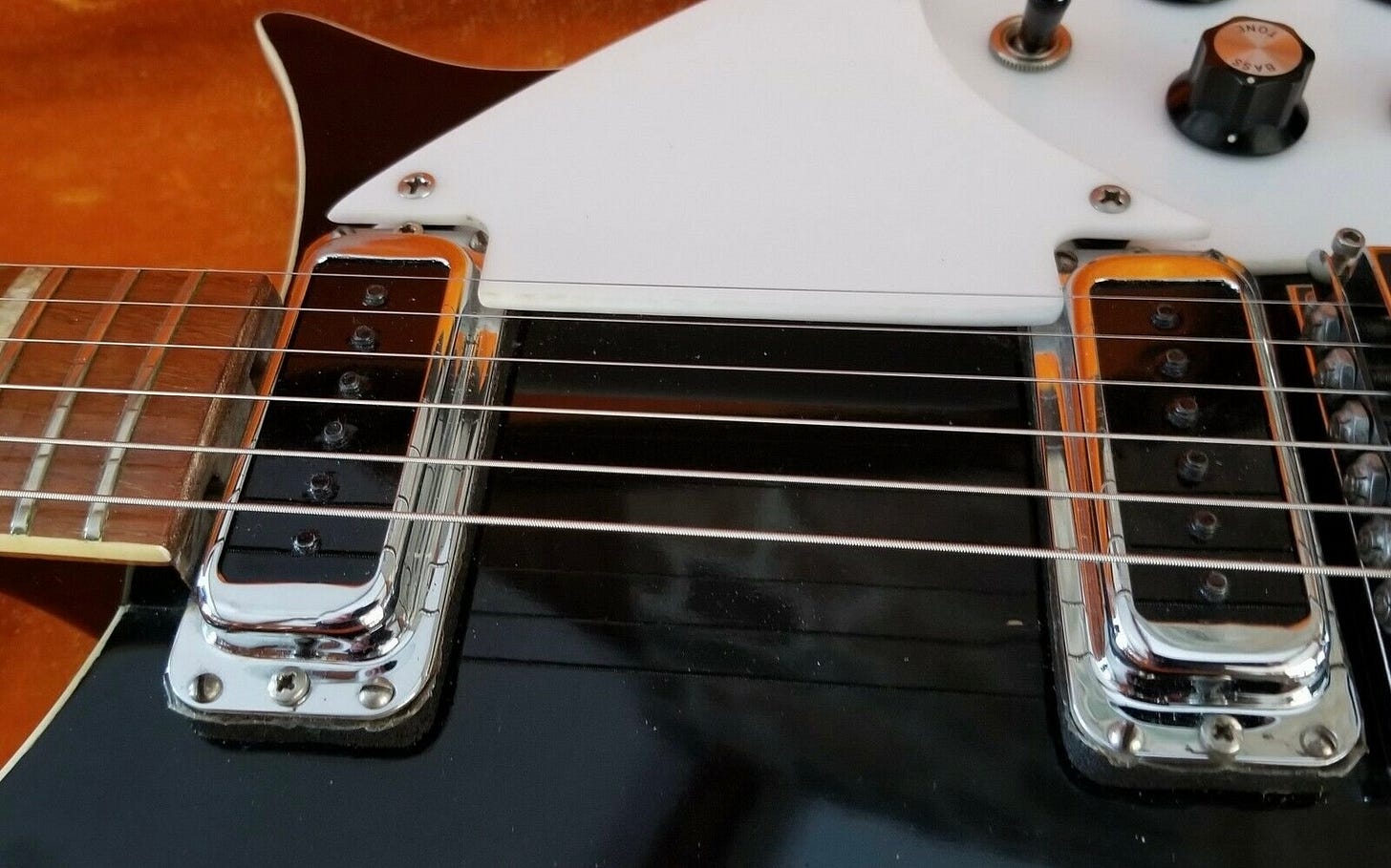
Guitars from later in the year wore black painted button top Higains. To learn more about Higain pickups, click here.
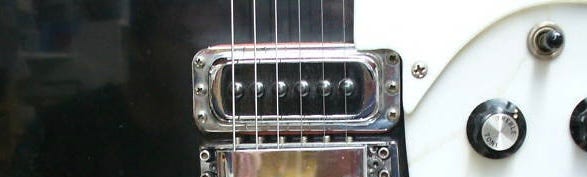
Around July the white phenolic nut changed back from white to black. And towards the end of the year, the full width crushed pearl triangle inlays transitioned to inset pearlescent poured resin.

1974
Starting in 1974, binding was added to the end of the fingerboard.
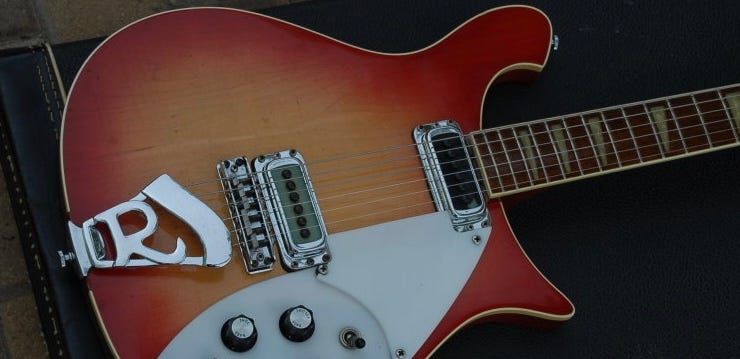
1976
In January the backpainted plexiglass truss rod cover found on all models was replaced by the raised letter injection molded truss rod cover in both white and black. These were made of an injection molded thermoplastic with the letters of the logo raised and painted, black for the white cover and white for the black cover. At launch most models had “MADE IN U.S.A.” AND “MODEL XXX”—in black or white as appropriate—stamped perpendicular to the logo, but smaller volume models like the 620 did not get the model number stamp, only “MADE IN THE U.S.A.”
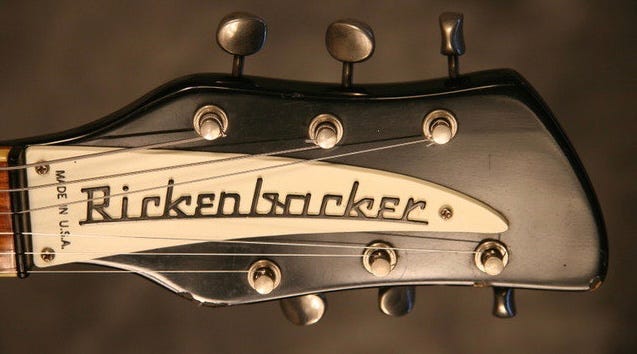
A model-specific change also occurred in 1976: the neck heel got longer.
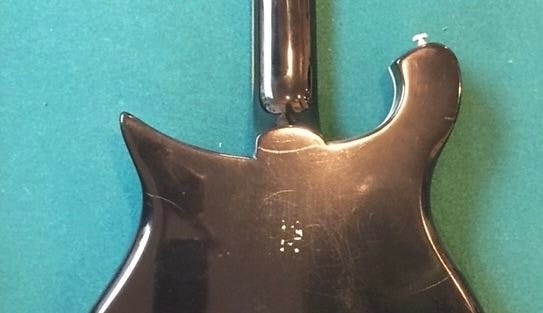
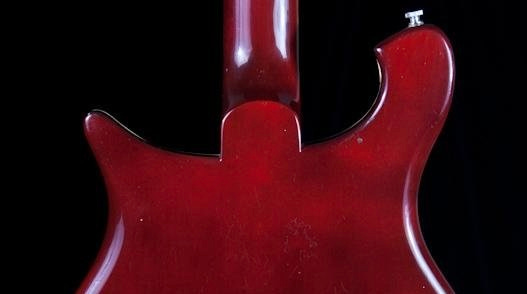
1979
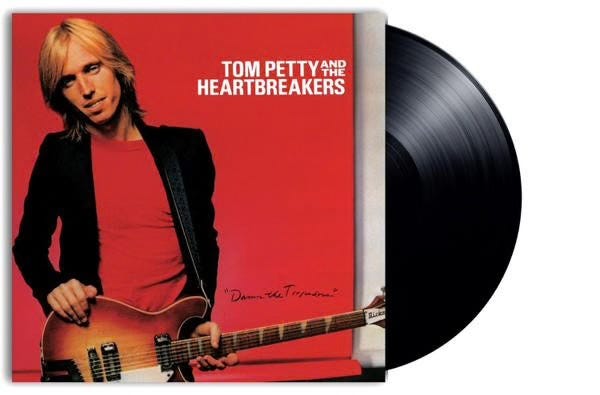
You want to know why the 620 is a “core” Rickenbacker model today? This. This right here. Rickenbacker (probably) made more 620s in 1980 ALONE than the entire previous decade. “Damn the Torpedoes” by Tom Petty and the Heartbreakers was released in October 1979, with Petty holding the 1963 625/12 prototype we talked about earlier on the cover, and the 620/12 went into main line production for the first time ever three months later in January of 1980. 6-string versions following right behind. And they never stopped.
You all know the story of how Mike Campbell came to own this guitar—how disappointed he was at first to find that the “Rickenbacker 12-string” he’d found in the classified ads was a solidbody. But if it had been a 330/12 or 360/12 Petty was holding on that record cover, it’s more than likely that the 620 would have been discontinued due to low sales along with the 450 after John Hall bought the company and rationalized the product line in 1985. That album cover is that important.
1980
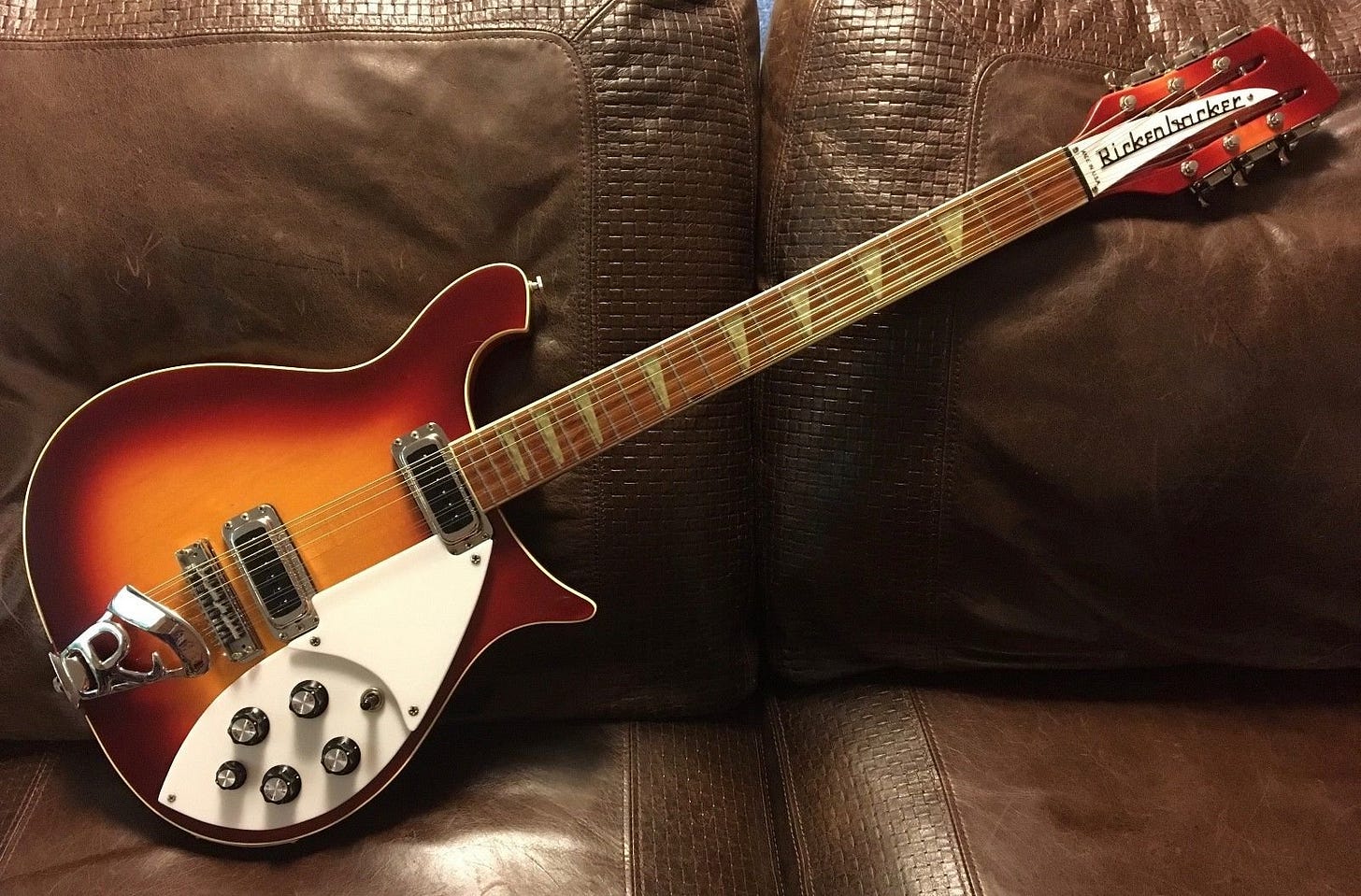
In January the 620/12 was launched as a production model in response to the sudden interest in the model. It was identical to the 6-string version apart from the obvious 12-string adaptation. And by June, production was high enough between the 620 and 620/12 that the 620 “earned” a model designation stamp on the truss rod cover—something its volume had not merited up to that point.
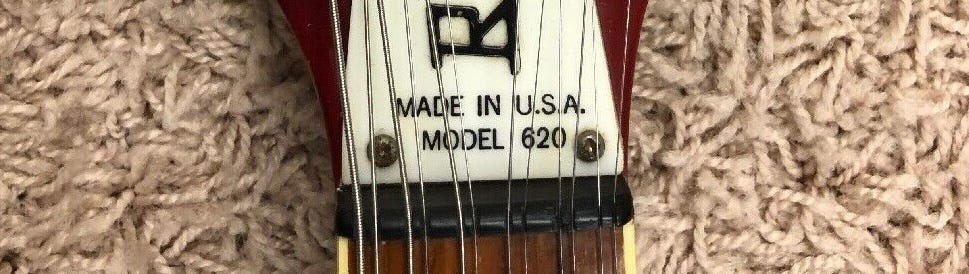
Here’s an oddity: a handful of April 12-string guitars featured two piece necks. Why? It wasn’t concern about neck strength—the 450 had always had a one piece neck with no issues. Maybe they didn’t have enough neck blanks. Maybe they were just testing it out as a potential cost saver. We’ll likely never know—but they do exist!
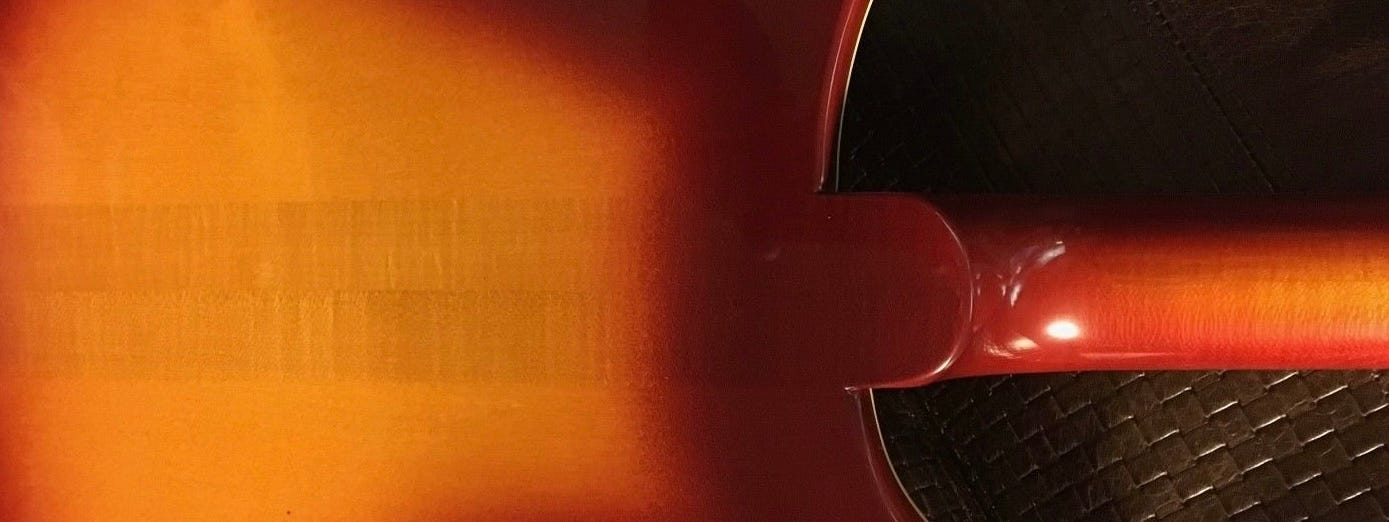
1982
John Kluson of Kluson Tuners died in late 1981, and when no buyer expressed interest in the company the decision was made by the family to close the doors. Which left Rickenbacker in a bit of a bind as the Kluson Deluxe was their primary guitar tuner.
At the time, Grover made a guitar tuner of similar construction to the infamous “wavy Grover” bass tuner with a not dissimilar footprint to the Kluson—and similar “bean” tuner heads. And so the “Slimline” or “box Grovers” began appearing on all guitars, including the 620, in mid 1982. From the front of the guitar, you can’t tell the difference. From the rear you absolutely can. By the end of 1982 this was the primary tuner on all vintage headstocks, and it would be until mid 1984.
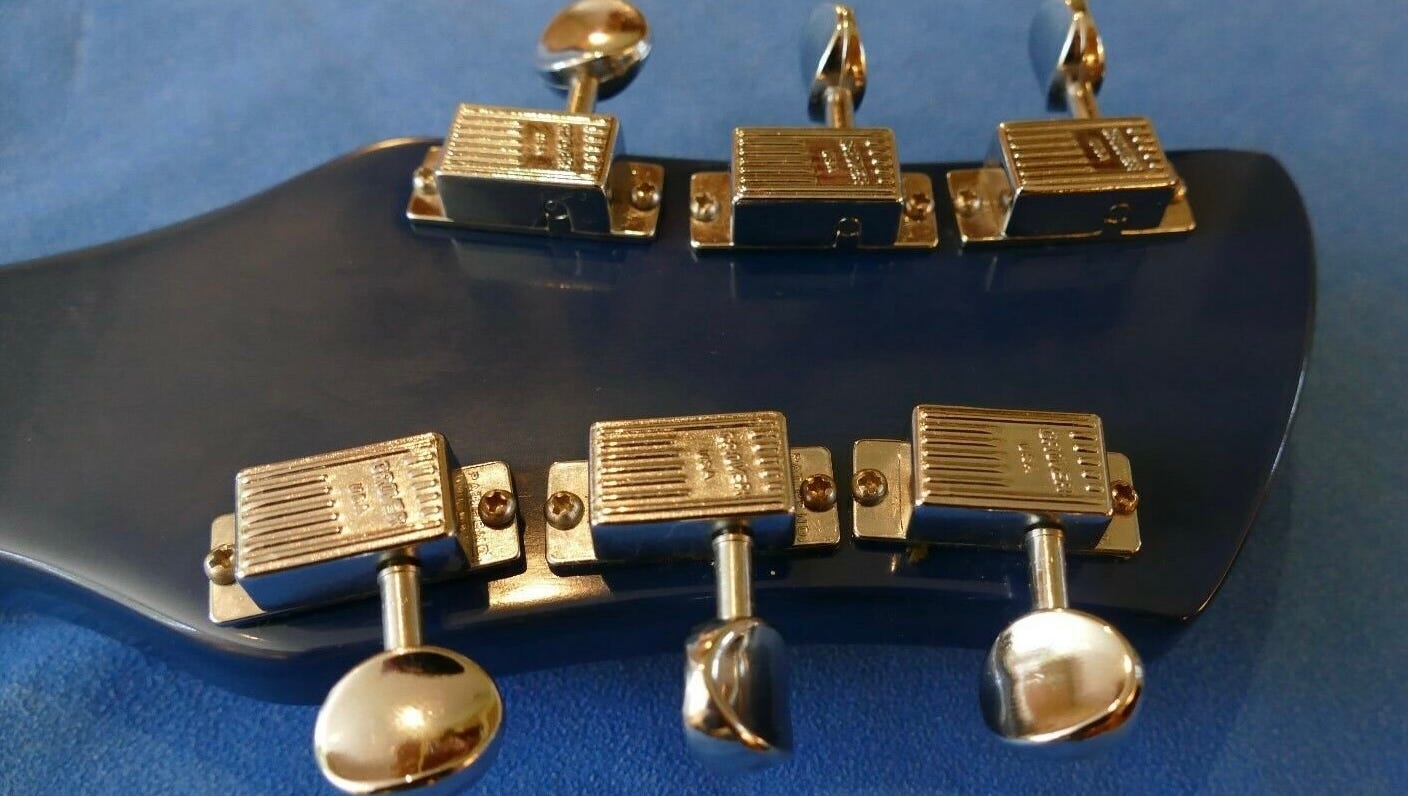
1984
A major change impacted the entire Rickenbacker guitar line, including the 620: an updated bridge design. The locking nut that had held the saddle adjustment screws in place since the bridge was developed in the 1950s was removed and replaced with a spring behind the saddle to achieve the same end. This slimmed down bridge would become the default on all models in January.
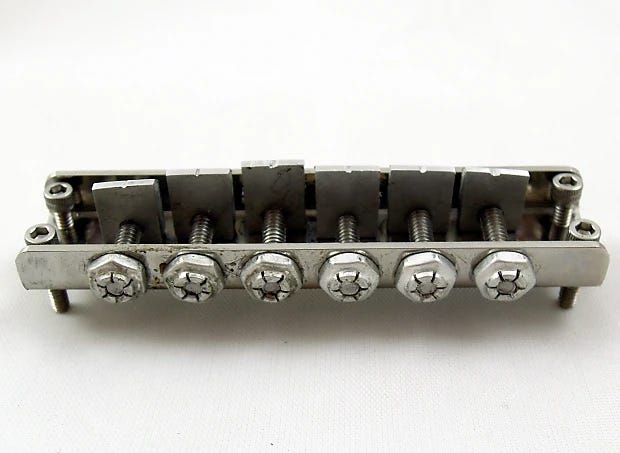
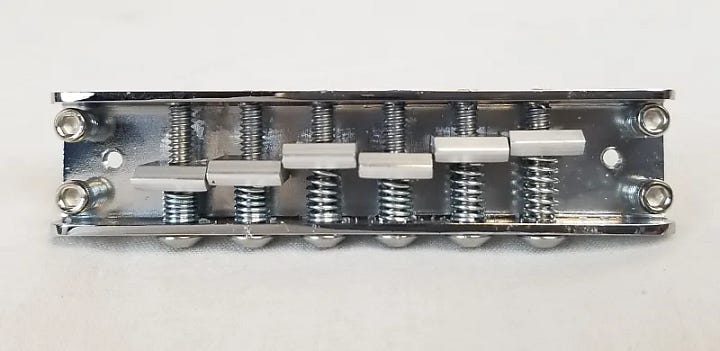
In early 1984, the Grover Slimline tuners currently in use were discontinued by Grover. While Rickenbacker worked on a permanent solution, the Grover Rotomatics in use on the 360 were used in place of the Slimlines. It looks strange to see Grover Rotomatics on a vintage style headstock, but during this period it is 100% correct!
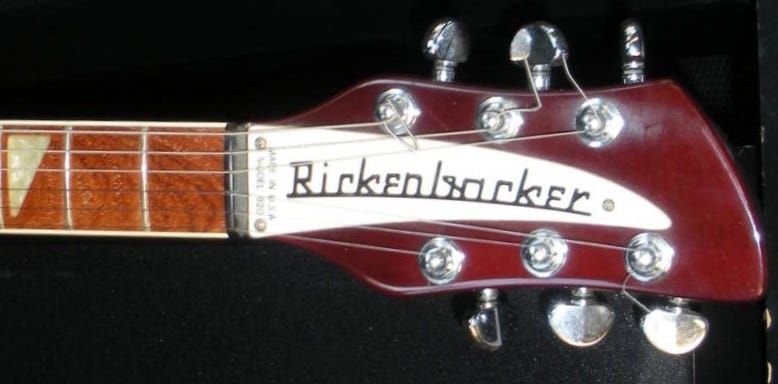
At some point in late 1984/early 1985, like all guitars the 620 would transition from the traditional Rickenbacker double hairpin truss rods to a pair of conventional single action truss rods. Neck construction would change slightly to accommodate—but only internally in the truss rod channel. The only way to identify which truss rod system is in place is to remove the truss rod cover.
At some point during the year, the “vintage tone circuit” (a high pass filter capacitor) that had been standard on all Rickenbacker guitars and basses since the 1950s was removed, giving the bridge pickup a higher output with more bottom end.
Towards the end of 1984 all models, including the 620, began losing the “model number” stamp on the truss rod cover. While you can find some model number TRCs into early 1985, by the middle of that year all models only had “MADE IN U.S.A.” truss rod covers.
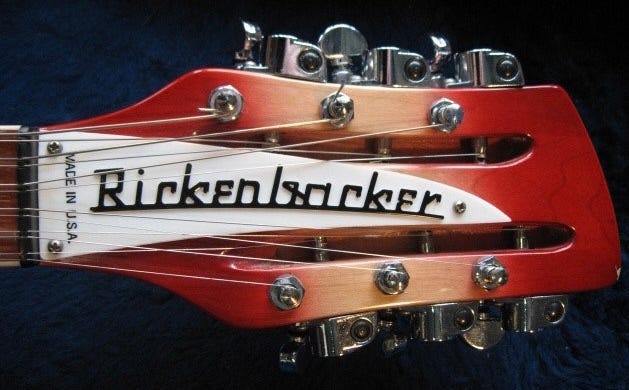
For the first time since 1969 the “Standard” 610 returned—although only briefly, as a special run for Japan. And it was a 12-string, for the first time in the model’s history. Only a handful were made, and the few that have surfaced have all been obviously modified so it is not certain what the original specs were.
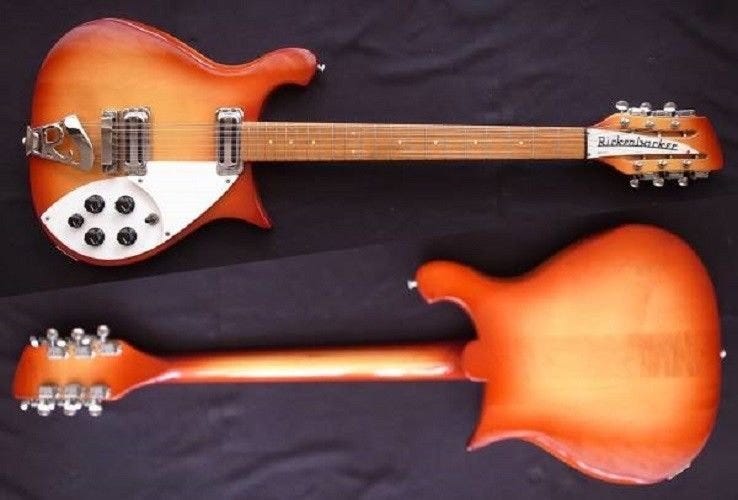
1985
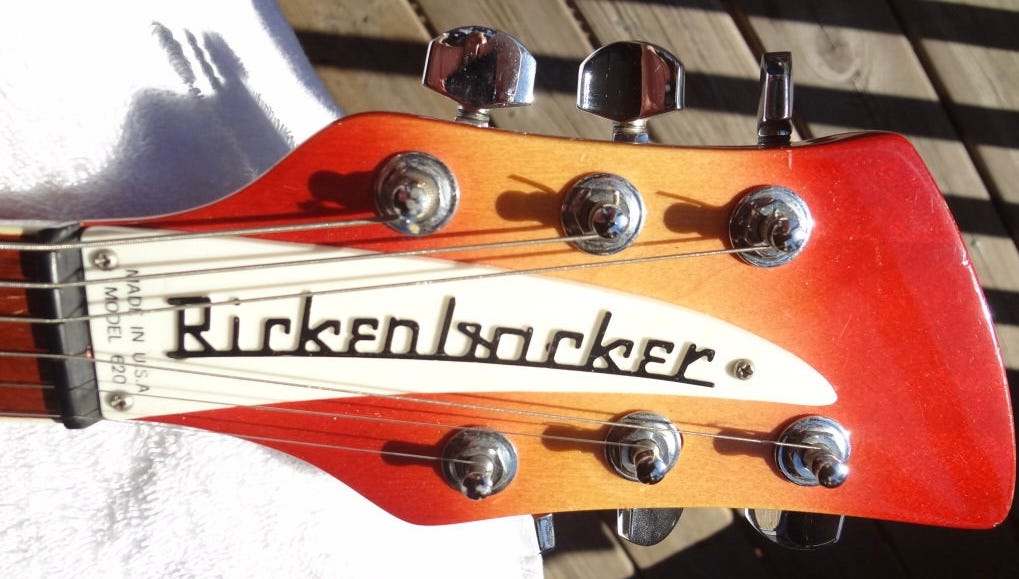
In late 1984 Rickenbacker began introducing Schaller M6 Mini tuners on all mainline guitars. In order to accommodate the larger bushing footprint of these tuners, the headstock was widened by about 1/2”—creating the so called “paddle” headstock. This combo first appeared on the 620 in March of 1985.
In general, late 1984-early 1985 Rickenbacker headstocks and tuners are a mess, with multiple combinations of tuners and headstocks found. No matter how weird it may look…it probably left the factory like that!
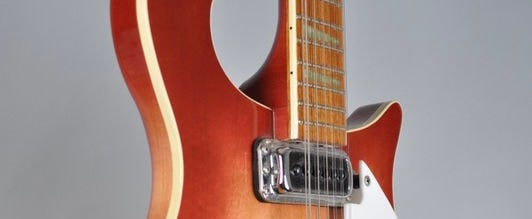
In the beginning of 1985, the binding at the bottom of the fretboard that had first appeared in 1974 disappeared for good.
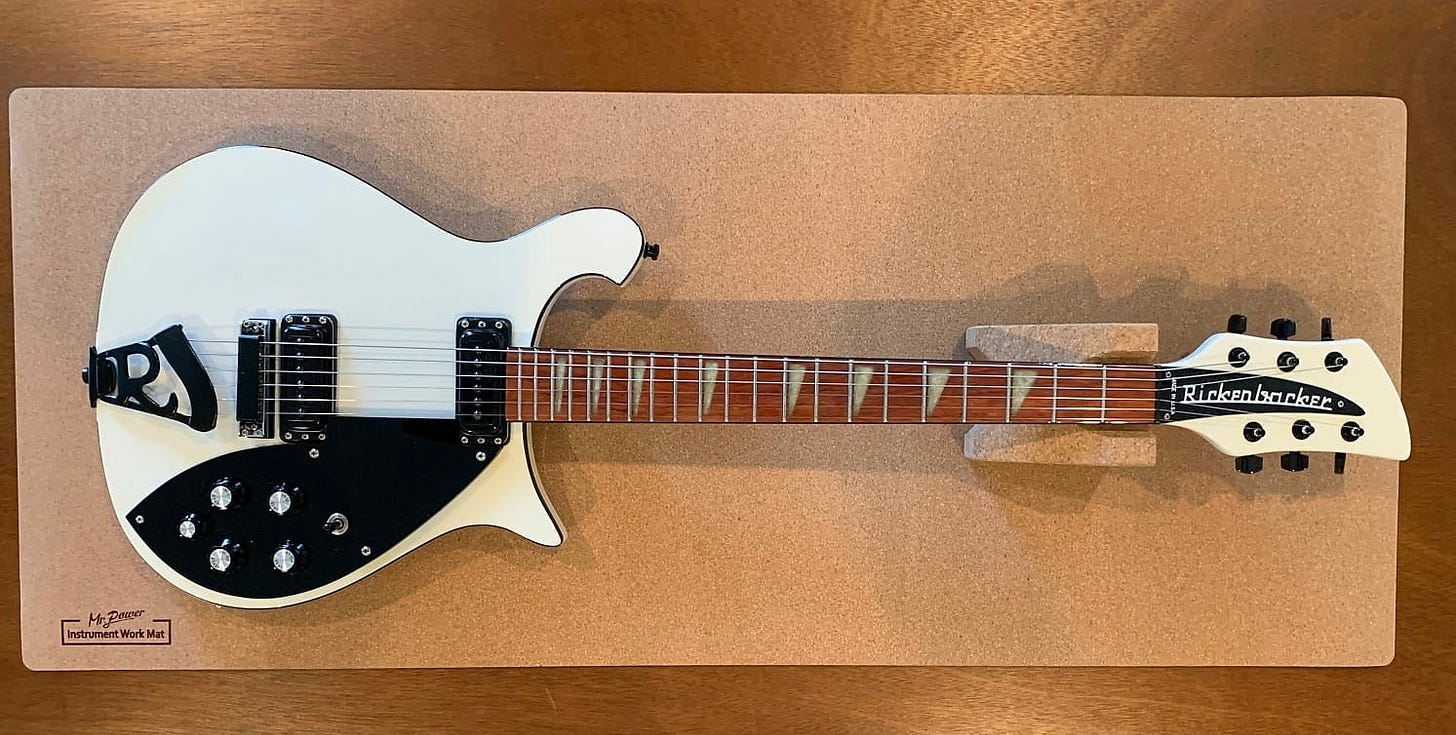
Mid 1985 marked the beginning of the BH/BT (black hardware/black trim) era, with Midnight Blue, Red, White, Silver, and Mapleglo guitars equipped as standard with black finished tuners/pickup covers/bridges/strap pins/serial number plate and black plastic binding/pickguard/truss rod cover.
1986

The 600 series regained a “standard” version for the first time since 1969 with the introduction of the 610. Just like the 1960s 615, the 610 lost its Deluxe 620 brother’s binding, triangle inlays, and stereo wiring, and gained a contoured top that made it more comfortable to play. All the other features were identical to the 620.
1987

The 610 got 6 more strings with the launch of the 610/12, although it did not appear on the pricelist until 1988. All other features were identical to the 6 string version.
1991
A minor change to all Higain equipped guitars—including the 620–occured around August. A new dual-use pickup bobbin was introduced for use on both Higain and toaster pickups—ending the “fiberboard” button-top Higain era. Click HERE to learn more about how to identify Higain pickups.
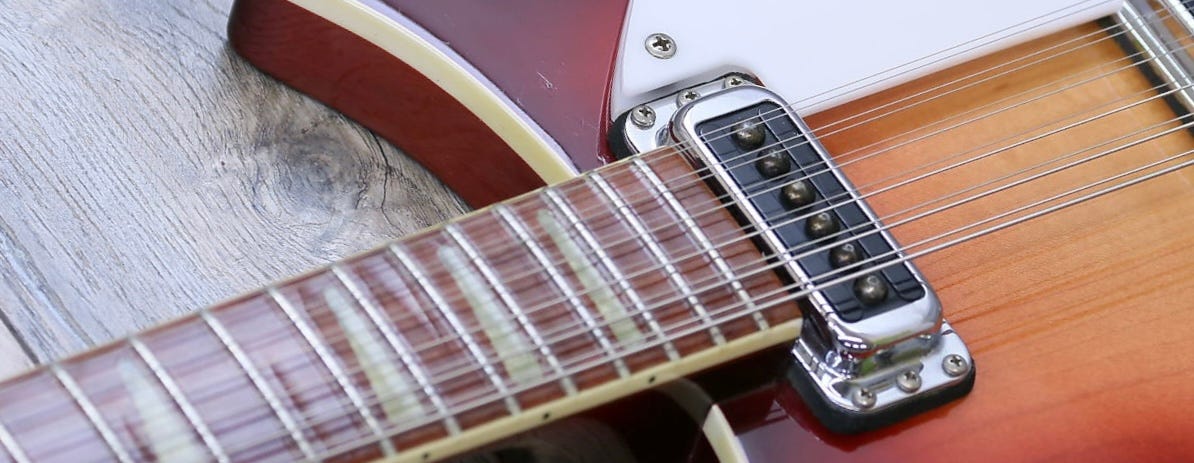
1995
Around July, all non-vintage/reissue guitars—including the 620–moved away from the vintage reeded edge strap button that had been used since the late 50s. It was replaced with a Schaller strap lock button, albeit still attached to the Rickenbacker style bolt instead of the “stock” wood screw. While the supplier has changed over the years, the style remains in use to this day. The reeded bolt is still used on vintage/reissue guitars, and as the mute adjustment screw on bass bridges.
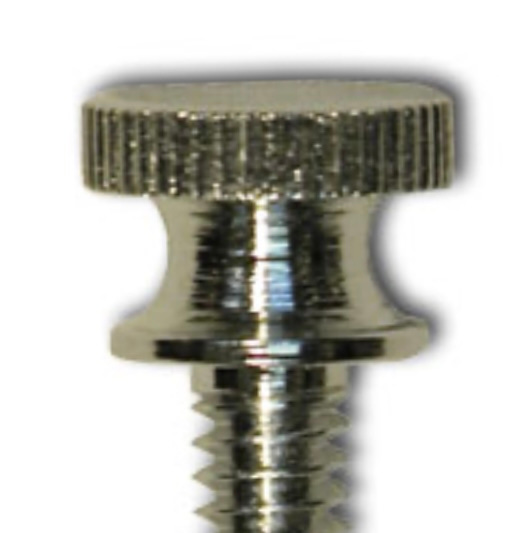
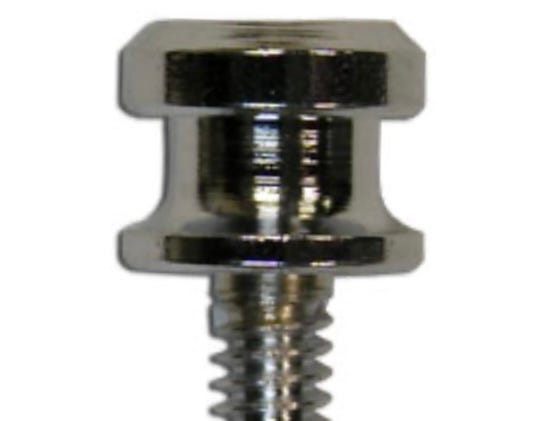
1996
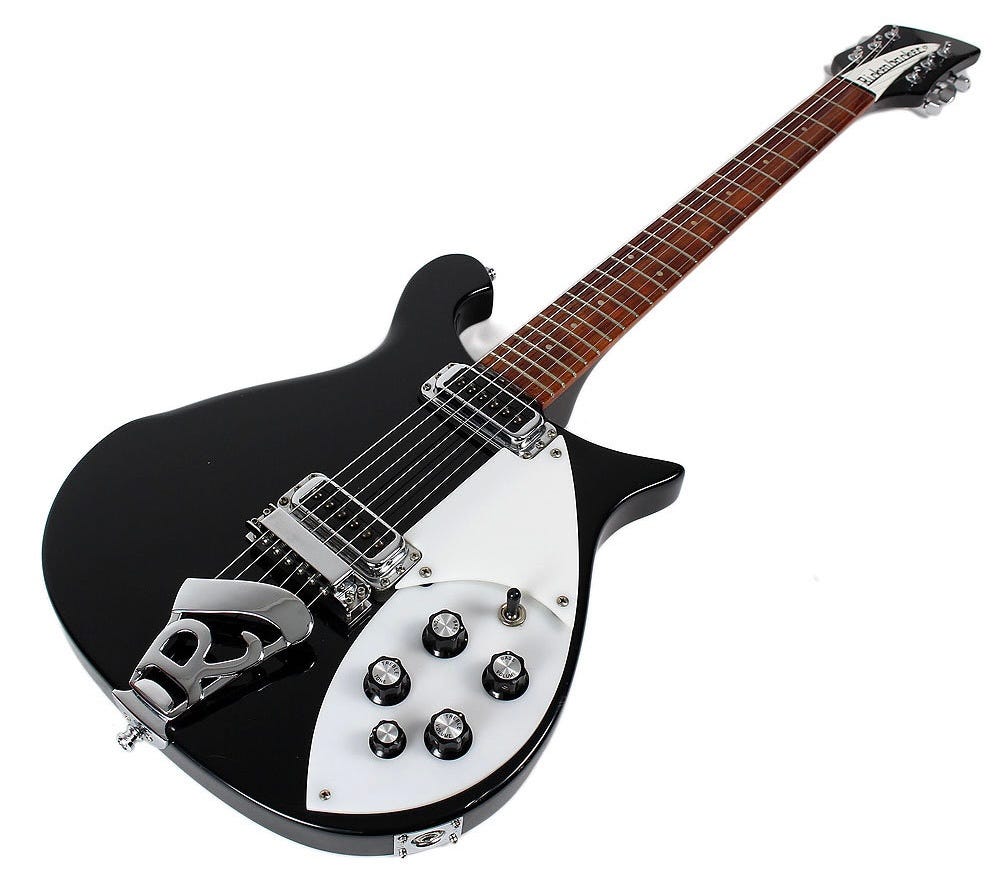
Probably more as a result of line rationalization than a substantial reduction in demand, the 610 and 610/12 were quietly discontinued at the end of the year.
A major change to the production process occurred in 1996 with the transition to CNC manufacturing. Prior to CNC machining, bodies and necks were hand cut using templates that wore over time, leading to slight variations from guitar to guitar and year to year as those templates wore and were replaced. Now the same shape would be cut every time. And not only was it more consistent, it was different.
The first CNC 620s appear to date to around November. The most noticeable change was to the cresting wave cutaway. The top of the horn was rounded over a bit, and the cutaway itself was a little deeper, leaving the point of the cresting wave more pronounced and the horn slightly thinner.
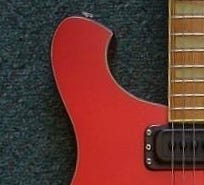
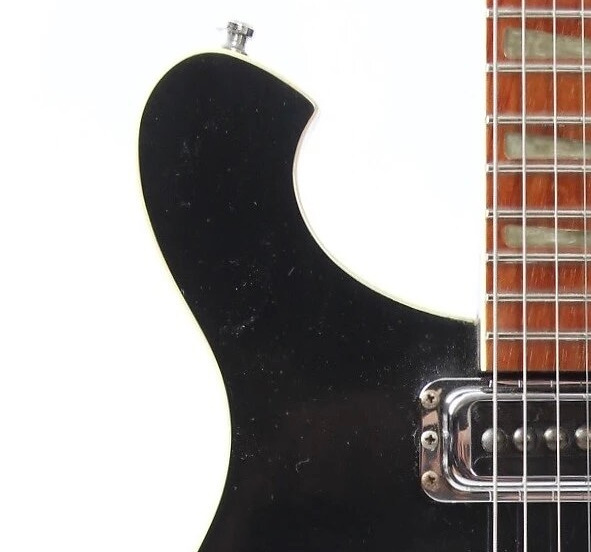
2003
in March 2003, shortly after “dimples” (to match the molding marks found on 63 and earlier toasters) were added to toaster pickups to help make the new C series guitars appear more authentic, Higains got dimples as well. They began appearing on the 620 in June
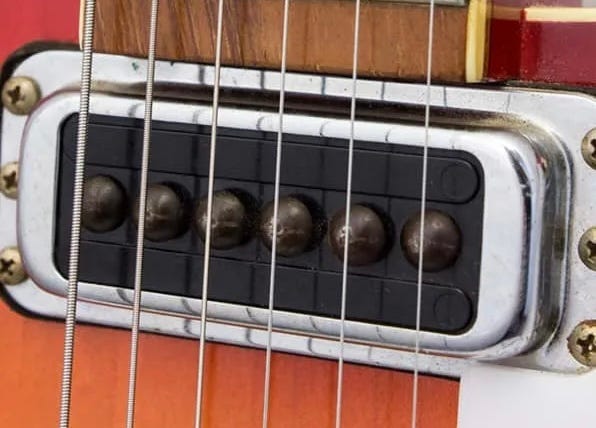
2005
In a nod to stringing convenience, beginning in June the sideways tuner “slots” on all non-vintage 12-strings were carried all the way through the headstock. The change made it to the 660/12 in October.
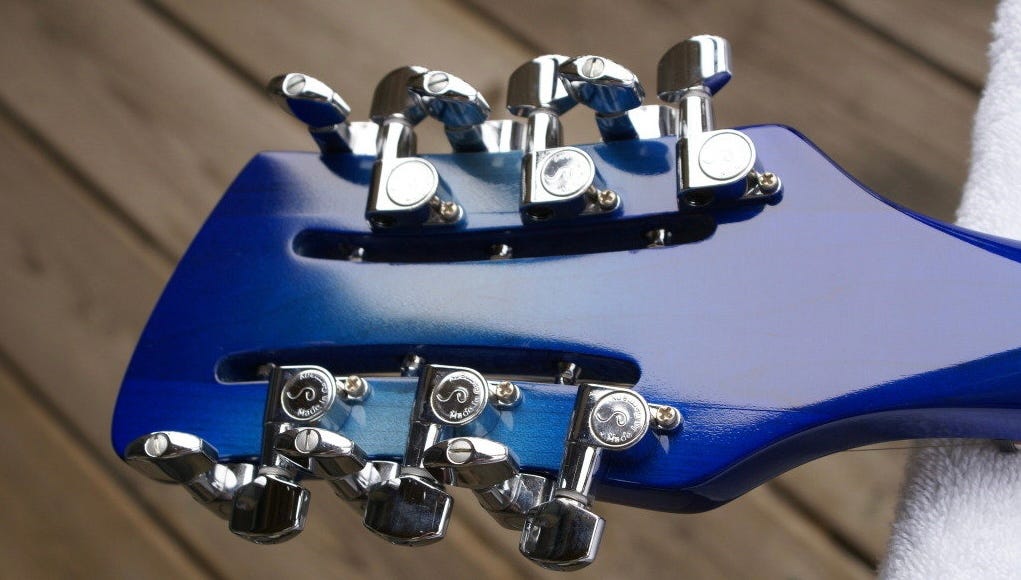
Around May of 2005, the button top drive screw polepieces that had been used on Higain pickups since 1973 were replaced by adjustable polepieces on all guitars. 620s with both button top and adjustable polepieces can be found from then through late 2006, but by 2007 the button tops were no more.
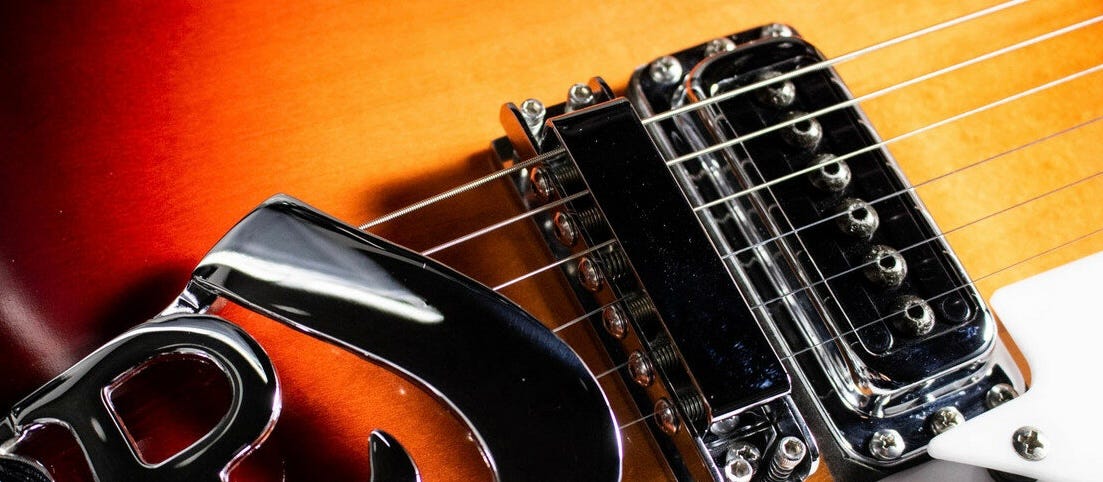
2007
The paddle headstock that first appeared in 1985 lost its extra half inch to return to roughly its original width—although the 620 headstock remains slightly wider than the one found on semi-hollowbodied guitars.
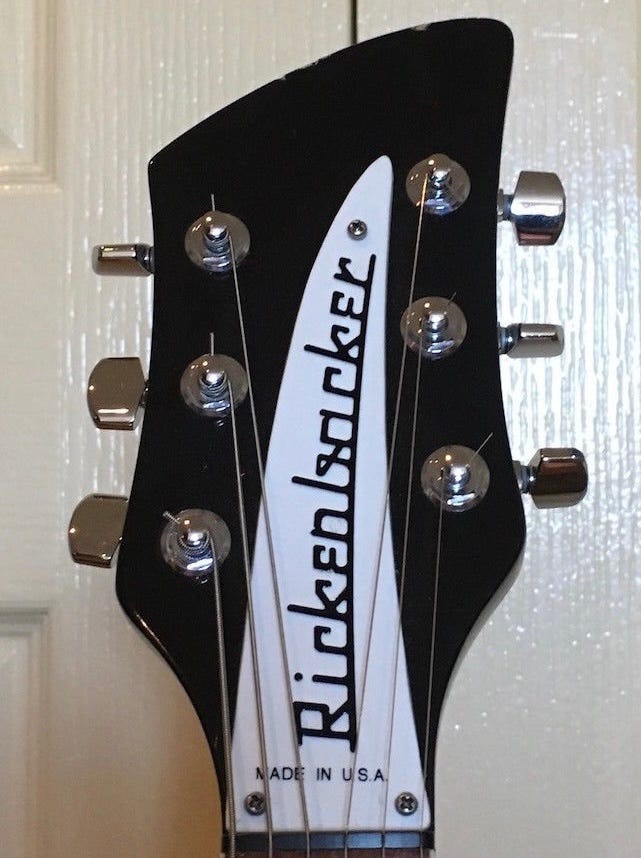
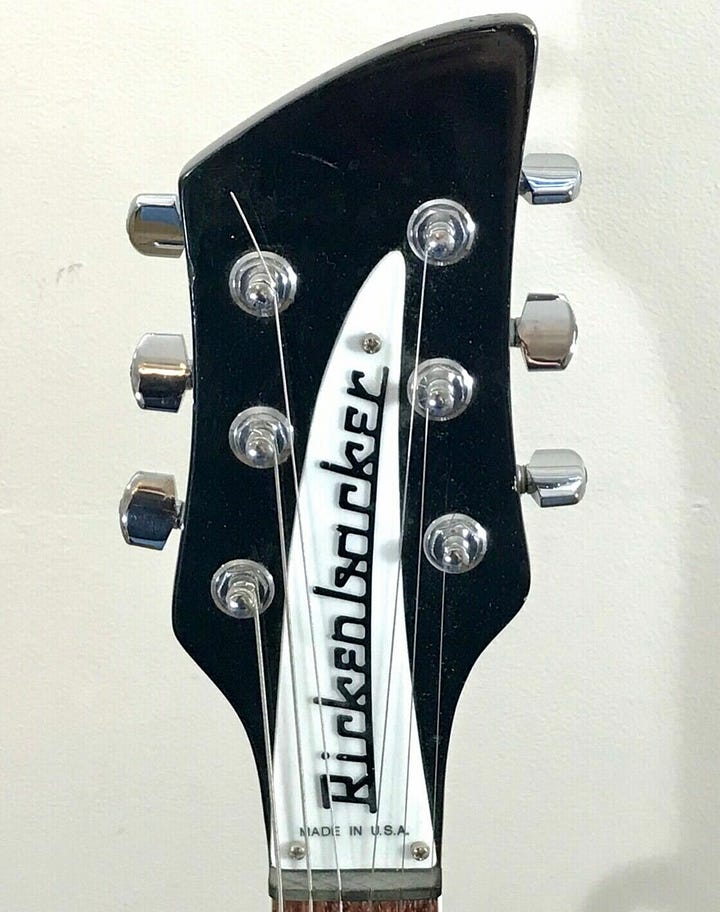
2008
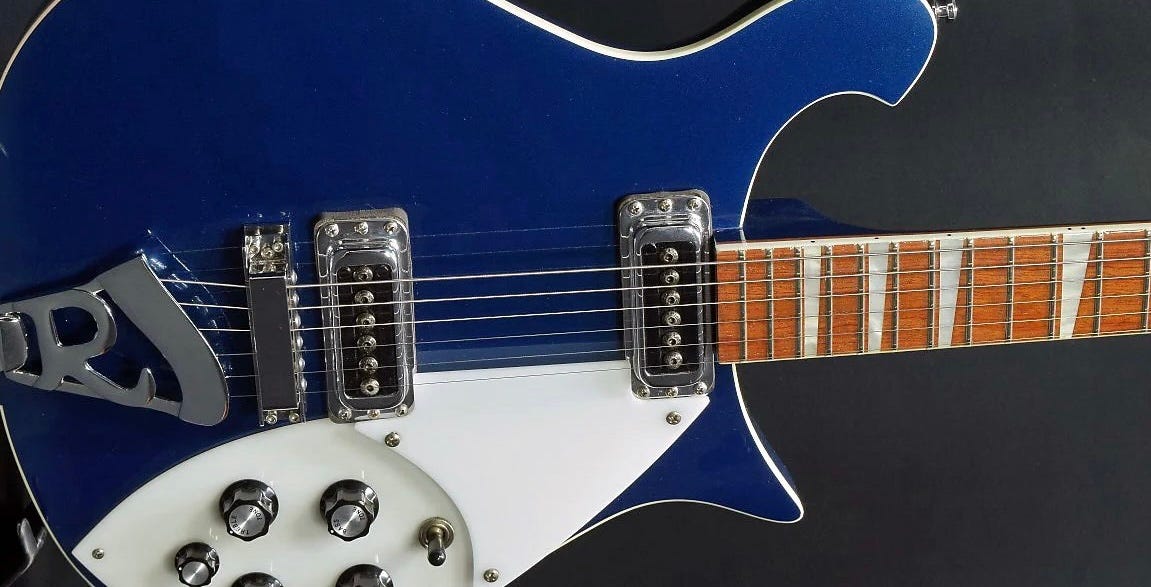
With much fanfare, the triangle inlays on the 620 and all “Deluxe” Rickenbackers reverted to full width triangle inlays for the first time since 1973…although in pearloid acrylic instead of crushed pearl.
2009
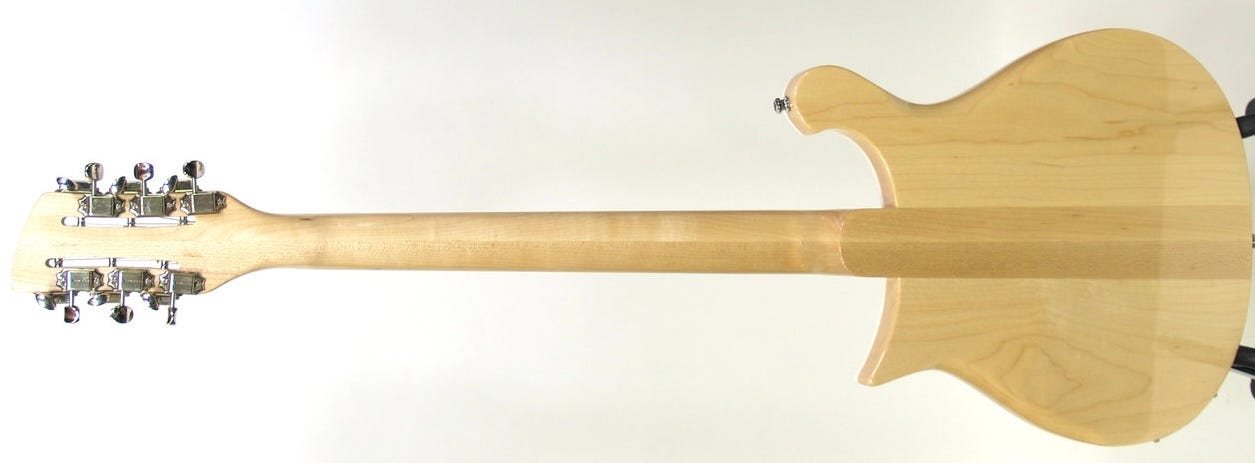
(Probably!) as a cost savings measure, all solidbodied Rickenbacker guitars, including the 620, moved from a one-piece to a two-piece neck.
While the cresting wave cutaway had been slightly rounded over during the CNC transition in 1996, a 2009 tweak to the 620’s CNC program finished the job, completely rounding over the horn and removing any link back to the original Combo 400’s tulip shaped upper horn.

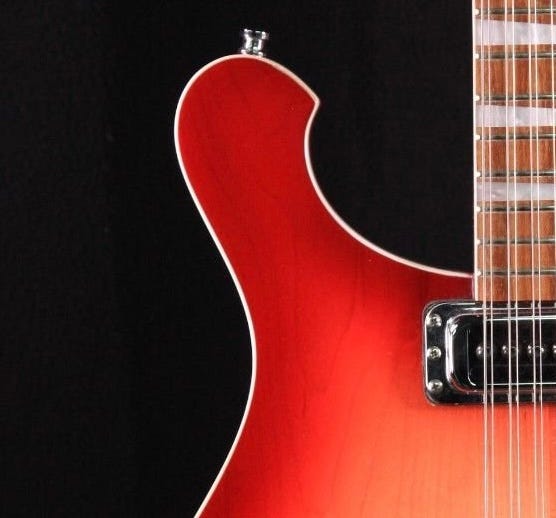
2011
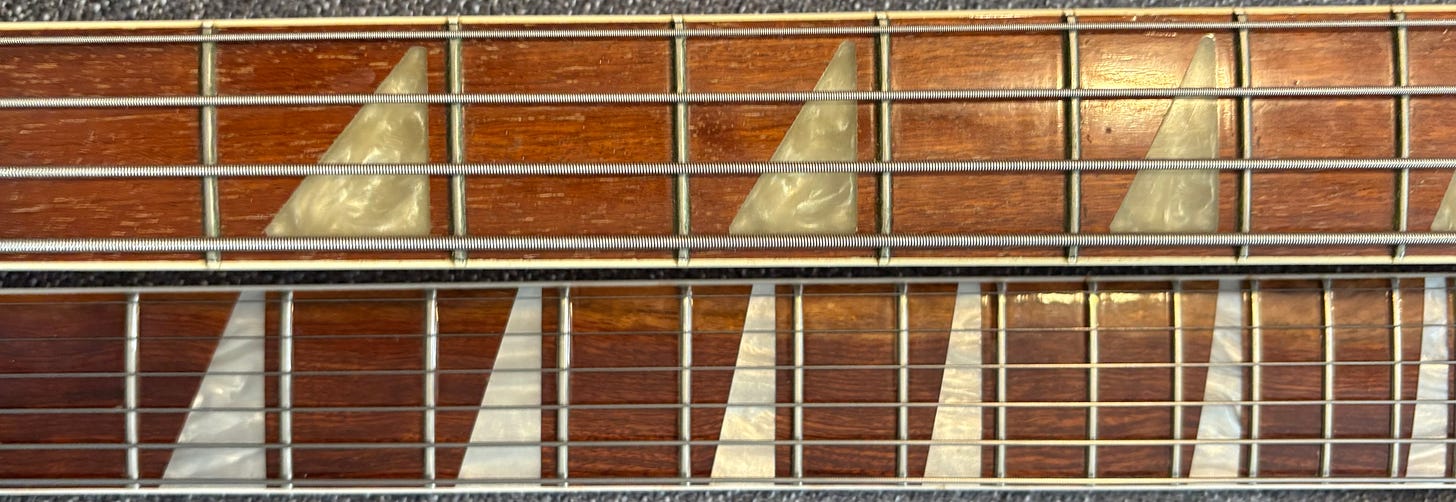
There is much debate (and misinformation) about the wood Rickenbacker has used for their fingerboards. While the company has always used the generic “rosewood” terminology, the specific genus and species used has changed over time. Consequently, “bubinga” or “African rosewood” are the terms most commonly used to describe the fairly evenly colored, tightly grained, fairly porous and slightly reddish boards historically used.
In late 2011 that changed to chechen, a Caribbean rosewood. Chechen is browner, has more color variation, a more charactered grain, and a less porous grain, meaning there is much less white grain fill used on the boards—that grain fill being a defining part of the Rickenbacker board “look” in many people’s eyes
2012
A very subtle change was made to the “MADE IN U.S.A.” font on all raised letter truss rod covers. The new font is a little “squarer” and more “compact”.
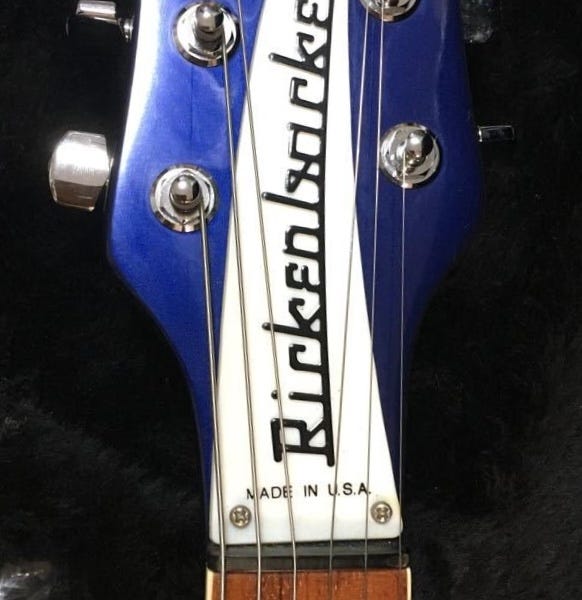

2020
Whether it was a conscious decision or a COVID supply chain issue that just became permanent, the silver topped knobs that had been standard on all core Rickenbacker models since 1965 began phasing out across the entire line. By the end of the year, black “vintage” knobs became standard on all models, including the 620.
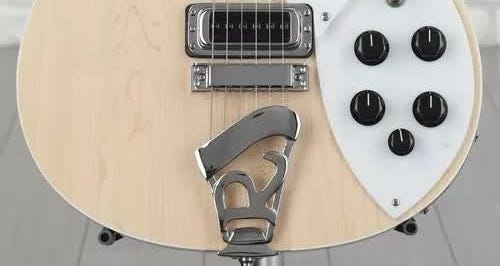
2021
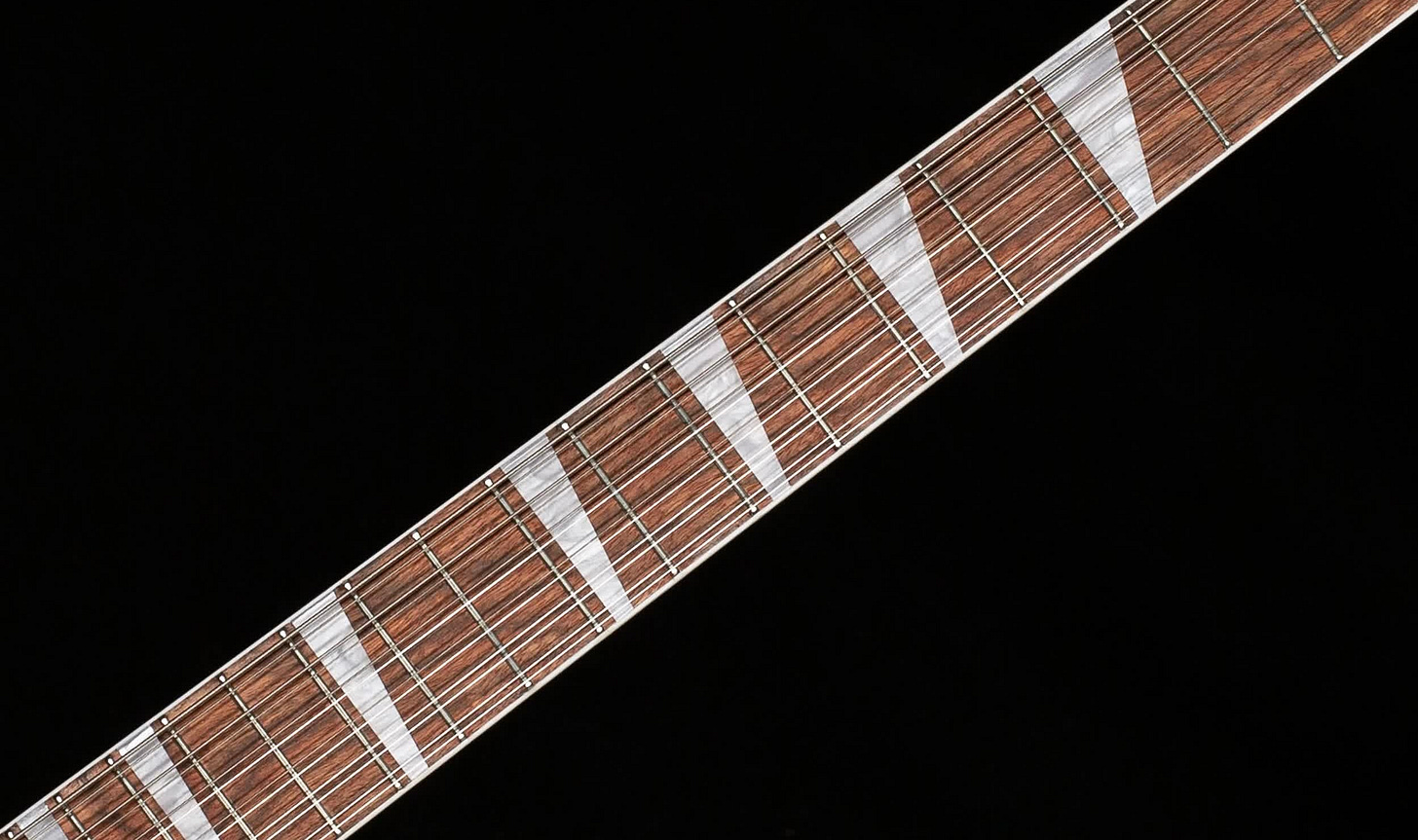
In August a monumental change took place: fingerboards went from being finished to unfinished on all core instruments, including the 620.
That same month a new CNC program for the 620 fixed the rounded-over horn on the cresting wave cutaway, bringing it closer in appearance to the original design.
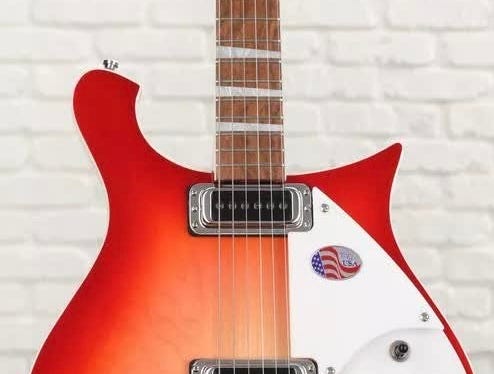
2022
Around September Rickenbacker quietly began finishing fingerboards again, ending a brief and unsuccessful experiment.
2023
In mid-year the tuners changed from the Schaller M6 Mini to a Gotoh M6 copy with the Rickenbacker “R” tailpiece logo on the back.
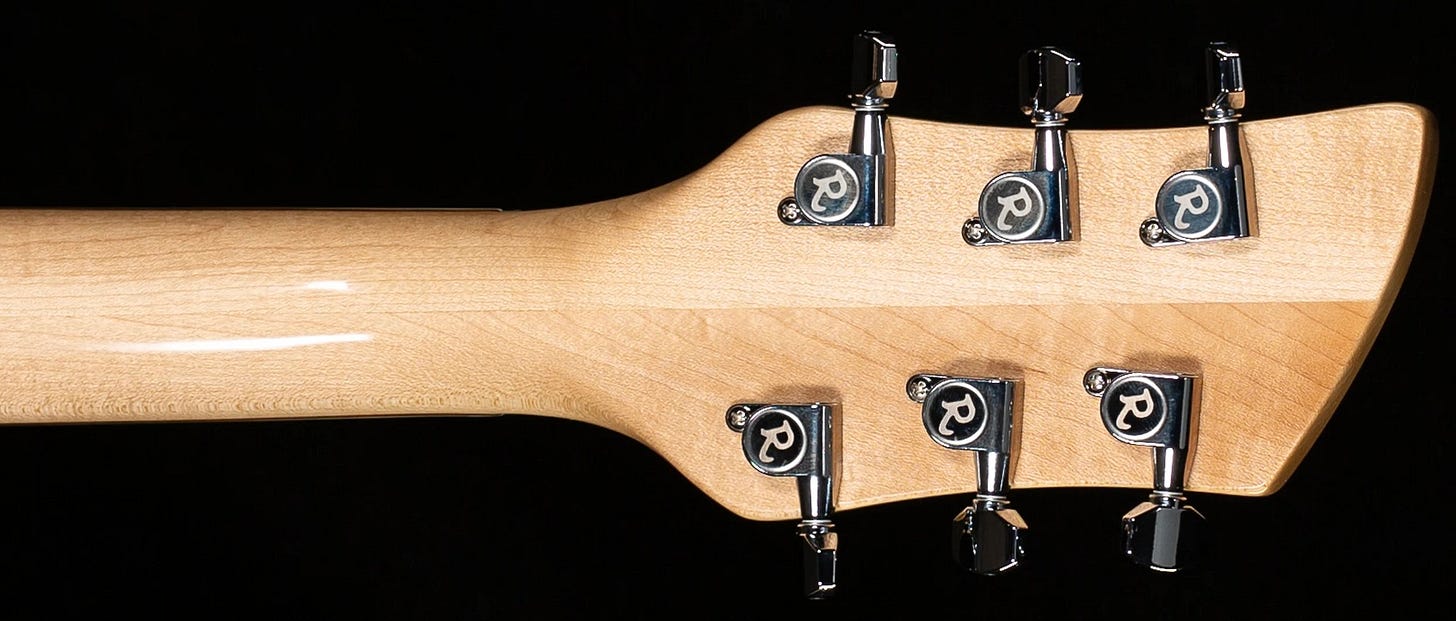
2024
The twin single action truss rods for all non C-Series guitars were replaced by a single, dual action truss rod. The change can only be seen by removing the truss rod cover.
And that brings us up to date with the luckiest model in the Rickenbacker line. Let me know if I missed anything!
I had a '62 625/6 back in 1963 when I was a kid and it was the most beautiful guitar I had ever seen or played. I was afraid to ding it by bringing it to garage band practice. I eventually moved on to a 330/6 and then a 360/6. It took working a couple of jobs to pay for them and I had to sell the previous one, but I had a Rickenbacker and that was sublime. 625 was the best beginner guitar ever.
Outstanding compilation! Fun to read AND see!